Understanding Hydraulic Quick Couplers: Types, Uses, and Choosing the Right Coupling - Bonovo
Hydraulic quick couplers are essential components in countless industries, dramatically speeding up the process of connecting and disconnecting hydraulic lines. Whether you're operating heavy construction equipment, agricultural machinery, or managing industrial hydraulic systems, understanding the different types of hydraulic quick couplers and how they work is crucial for efficiency, safety, and preventing costly downtime. This article dives deep into the world of hydraulic couplers, exploring the various types available, their specific applications, key selection criteria like pressure ratings and thread types, and maintenance tips to ensure a reliable connection every time. If you rely on hydraulic tools and attachments, knowing about quick coupling technology is key to maximizing your operational performance.
1. What Exactly is a Hydraulic Quick Coupler and Why Use One?
A hydraulic quick coupler (often called a quick coupling or simply coupler) is a specialized fitting designed to quickly connect and disconnect hydraulic lines without the need for tools and with minimal loss of hydraulic fluid. Think of it as a convenient "plug and play" system for your hydraulic system. The primary purpose of these couplers is to dramatically reduce the time it takes to switch between different hydraulic tools or attachments on machinery like excavators, skid steer loaders, or tractors. This speed translates directly into increased productivity on the job site.
Imagine needing to switch an excavator from a digging bucket to a hydraulic hammer. Without a quick coupling system, this involves manually unbolting hoses, dealing with potential spillage, and carefully reconnecting lines, a process that can take significant time and effort. With a hydraulic quick coupler, the operator can often make the switch in minutes, sometimes without even leaving the cab. This ease of use is a major advantage, minimizing downtime and keeping projects on schedule. Furthermore, hydraulic quick couplers are designed to minimize air inclusion and fluid loss during connection and disconnection, protecting the integrity of the hydraulic system and the environment.
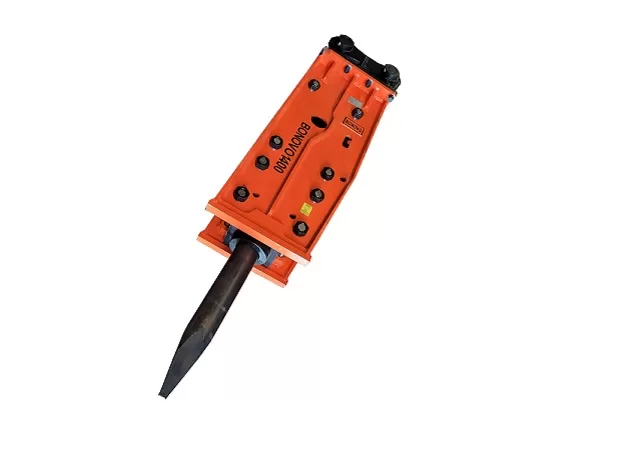
2. How Do Hydraulic Quick Couplers Function?
At its core, a hydraulic quick coupler consists of two main parts: a male half (plug) and a female half (socket or coupler). Each half is typically attached to the end of a hydraulic hose or directly to a component. Inside each half, there is usually a valve mechanism. When the coupler halves are disconnected, these valves automatically close, sealing the hydraulic line and preventing hydraulic fluid from leaking out and dirt or contamination from entering the hydraulic system. This internal shut-off system is critical for maintaining system cleanliness and preventing fluid loss.
When connecting the coupling, the male plug is inserted into the female socket. As they engage, the valves within both halves push against each other and open simultaneously, creating a flow path for the hydraulic fluid under pressure. Different types of hydraulic quick couplers use slightly different mechanisms (like locking balls, sleeves, or thread connections) to secure the two halves together, ensuring a reliable connection that can withstand the operating pressure of the hydraulic system. The process to connect and disconnect hydraulic hoses is therefore made simple and efficient, typically involving pushing the halves together or operating a locking sleeve or thread.
3. What are the Main Types of Hydraulic Quick Couplers Available?
There isn't just one type of hydraulic quick coupler; many types exist, each suited for different hydraulic applications and operating conditions. Understanding the common types is the first step in selecting the right coupler for your needs. The various types of hydraulic couplers primarily differ in their internal valve design and locking mechanism. Choosing the correct type of coupler is crucial for performance and safety.
Here are the three most prevalent categories of hydraulic quick couplings:
- Poppet Valve Couplers: These are a traditional and widely used type of hydraulic coupler. They use a simple poppet valve that is pushed open upon connection.
- Flat Face Couplers: Also known as flat-face or dry-break couplers, these are designed to minimize spillage and contamination. The mating surfaces are flat, making them easy to clean.
- Threaded or Screw-to-Connect Couplers: These couplers use a thread mechanism for connection, providing a very secure and vibration-resistant coupling, often used in high-pressure applications.
We will explore each of these types of hydraulic quick couplers in more detail below.
4. Poppet Valve Couplers: What are the Pros and Cons?
Poppet valve couplers are one of the oldest and most common types of hydraulic couplers. Their design features a cone-shaped or ball-shaped poppet valve held shut by a spring. When the male and female halves of the coupling are connected, the tips of the opposing poppets meet, pushing each other off their seats and allowing fluid to flow. Disconnecting the coupler allows the springs to reseat the poppets, theoretically sealing the hydraulic line.
Pros:
- Cost-Effective: Generally less expensive than other types of hydraulic quick couplers.
- Widely Available: Due to their long history, they are available in many different sizes and configurations.
- Good Flow Characteristics: Often offer relatively low restriction to hydraulic fluid flow.
Cons:
- Spillage Potential: Some fluid loss is common during connection and disconnection as the poppets move.
- Contamination Risk: The exposed poppet design can trap dirt when disconnected, potentially introducing contamination into the hydraulic system upon reconnection. Air inclusion can also be an issue.
- Connection Difficulty under Pressure: Connecting poppet valve couplers can be difficult if there is trapped residual pressure in the hydraulic line.
While still used in many hydraulic applications, especially in agriculture, the potential for spillage and contamination means they are often superseded by flat face couplers in more demanding or environmentally sensitive applications.
5. Why are Flat Face Couplers Often the Preferred Choice?
Flat face couplers, sometimes called flat-face quick couplings or dry-break couplers, represent a significant advancement in hydraulic quick coupler technology. As the name suggests, their mating surfaces are flat when disconnected. This flat face design offers several key advantages over traditional poppet valve couplers, making them increasingly popular, especially in construction equipment and industrial settings. The flat face type is specifically engineered to prevent leakage and contamination.
Key Advantages of Flat Face Couplers:
- Minimal Spillage: The flat face design allows for virtually no hydraulic fluid loss during connection and disconnection. This is better for the environment and workplace safety.
- Reduced Contamination: The flat surfaces are easy to wipe clean before connecting, significantly reducing the risk of introducing dirt, debris, or water into the sensitive hydraulic system. This is a major benefit for system longevity.
- Minimized Air Inclusion: The design helps prevent air from entering the hydraulic line during coupling.
- Ease of Connection: Many flat face couplers are designed for easier connection, even with some residual pressure (though connecting under zero pressure is always recommended best practice).
- Compliance with Standards: Many flat face hydraulic couplers adhere to ISO 16028 standards, ensuring interchangeability between different manufacturers' couplers that meet the same standard.
While often having a higher initial cost than poppet couplers, the long-term benefits of reduced fluid loss, minimized contamination, and enhanced hydraulic system protection often make flat face couplers the more economical and reliable choice for demanding hydraulic applications. Flat face couplings are becoming the standard in many industries.
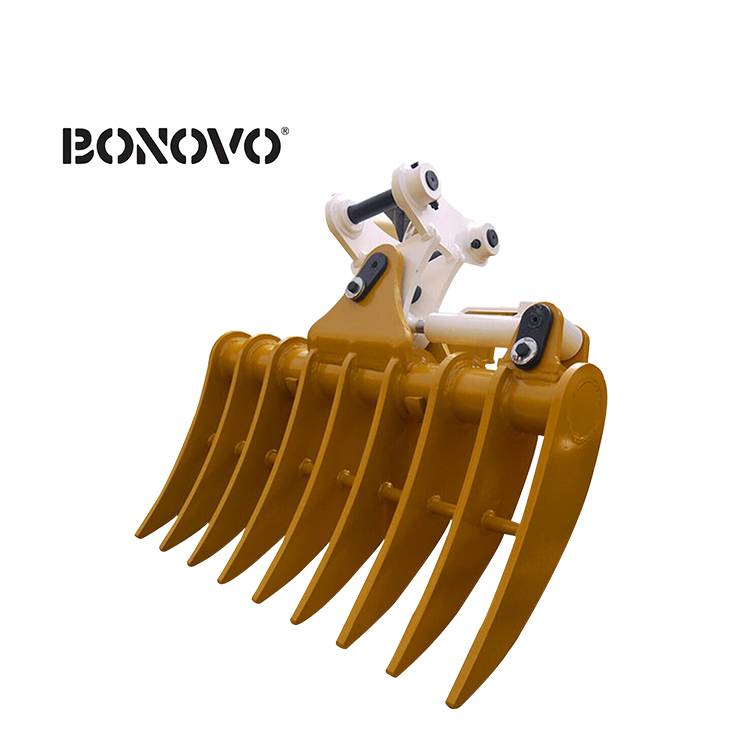
6. When Should You Use Threaded or Screw-to-Connect Couplers?
Threaded hydraulic couplers, also known as screw-to-connect couplers or screw couplings, offer the most secure type of quick connection. Instead of a push-to-connect sleeve, these couplers feature male and female threads that are screwed together to establish the coupling. This screw to connect mechanism provides exceptional resistance to accidental disconnection caused by vibration, impacts, or hydraulic impulses (pressure spikes).
These couplers are designed for specific demanding situations:
- High-Pressure Hydraulic Systems: The robust threaded flat face connection can handle extremely high operating pressures and pressure impulses often found in heavy demolition equipment (like hydraulic breakers or pulverizers) or specialized industrial machinery.
- High Vibration Environments: Standard quick couplers might vibrate loose over time; the thread connection prevents this, ensuring a continuous and reliable connection.
- Trapped Pressure Connection: Some screw-to-connect couplers are specifically designed to be connected even against significant trapped pressure in the hydraulic line, which can be very difficult with other coupler types.
- Safety Critical Applications: Where accidental disconnection could be catastrophic, the positive locking action of the thread offers an extra layer of security.
While the connection and disconnection process takes slightly longer than push-to-connect couplers due to needing to turn the thread, the unparalleled security and ability to handle extreme pressure and vibration make threaded flat face couplers essential for certain heavy-duty hydraulic applications, including those involving concrete pulverizers or large hammers. The screw to connect design ensures maximum connection integrity.
7. What Key Factors Determine the Right Hydraulic Coupler Choice?
Selecting the correct hydraulic quick coupler involves considering several critical factors beyond just the basic type of coupler (Poppet, Flat Face, Threaded). Making the wrong choice can lead to leaks, premature wear, system inefficiency, or even dangerous failures. As manufacturers with extensive experience, like here at Bonovo, we always advise customers to carefully evaluate their specific needs. Mark Thompson, a typical fleet manager, would prioritize these factors to ensure his equipment runs smoothly and profitably.
Here's a checklist of key considerations for choosing the right hydraulic coupler:
- Operating Pressure: What is the maximum working pressure of your hydraulic system? The coupler must be rated for at least this pressure, including potential pressure spikes.
- Flow Rate: What is the required hydraulic fluid flow rate? The coupler's internal diameter and design affect flow; choosing an undersized coupler creates heat and inefficiency. Coupling size matters.
- Fluid Compatibility: Is the hydraulic fluid standard mineral oil, or is it a synthetic fluid, water glycol, or something else? The coupler's seal materials (like Nitrile, Viton, EPDM) must be compatible with the fluid.
- Port Size and Thread Type: The coupler's end connection must match the hydraulic hose or port it connects to. Common thread types include NPT, BSPP, ORFS, JIC. Mismatched threads will leak.
- Application Environment: Is the environment dirty, corrosive, or subject to high vibration? This influences the choice between poppet, flat face, or threaded flat face couplers and potentially the coupler material (steel, stainless steel, brass).
- Frequency of Connection/Disconnection: How often will the coupling be used? For frequent changes, the ease of use of flat face or push to connect poppet couplers is advantageous.
- Interchangeability: Do you need the coupler to connect with existing equipment? Checking for adherence to standards like ISO 16028 (for flat face) or ISO 7241 (common for poppet) is important.
- Minimizing Spillage/Contamination: Are environmental regulations strict, or is hydraulic system cleanliness paramount? If so, flat face couplers are strongly recommended.
Considering these factors carefully ensures you select a hydraulic coupler that provides a safe, efficient, and reliable connection for your specific hydraulic tools and machinery.
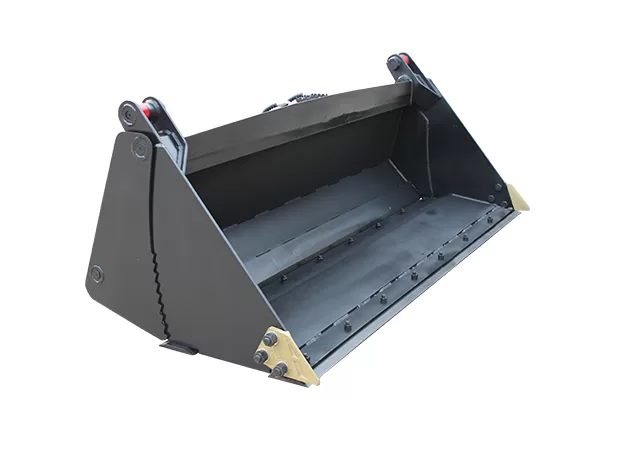
8. How Does Operating Pressure Impact Hydraulic Coupler Selection?
Operating pressure is arguably the single most critical factor when selecting a hydraulic quick coupler. Every hydraulic system operates within a specific pressure range, and the coupler chosen must be robust enough to handle the maximum system working pressure, plus a safety margin to accommodate potential pressure spikes or surges that can occur during operation. Using a coupler rated below the system pressure is extremely dangerous and can lead to catastrophic failure, potentially causing severe injury and equipment damage.
Standard couplers might be suitable for lower-pressure applications, but high-pressure hydraulic systems, common in heavy construction equipment like large excavators or demolition tools, require couplers specifically designed and tested for those demands. Threaded flat face or screw-to-connect couplers are often the go-to choice for very high pressure due to their secure thread mechanism. Flat face couplers are also available in various pressure ratings, including high-pressure versions. Poppet valve couplers generally have lower pressure ratings compared to the other two types.
Always check the manufacturer's specifications for the coupler's maximum working pressure rating and ensure it meets or exceeds your system's requirements. Never assume a coupler can handle the pressure based solely on its size or appearance. Mismatching pressure ratings is a common mistake that can have serious consequences for both operator safety and the longevity of the hydraulic system. The pressure rating is paramount for a safe and reliable connection.
9. Troubleshooting Common Issues: Maintaining Your Hydraulic Couplers
Even the best hydraulic quick couplers require proper care and maintenance to ensure longevity and optimal performance. Neglect can lead to leaks, difficulty connecting or disconnecting, and contamination of the hydraulic system, leading to the kind of downtime Mark Thompson actively seeks to avoid. Understanding common problems helps in prevention and troubleshooting.
Common Hydraulic Coupler Issues & Solutions:
- Leaks When Connected:
- Cause: Damaged internal valve or seal, worn coupling halves, incorrect thread engagement (threaded couplers), exceeding pressure rating.
- Solution: Inspect seals and mating surfaces for damage or wear. Replace damaged coupler halves or seals. Ensure threads are properly tightened. Verify system pressure.
- Leaks When Disconnected:
- Cause: Faulty internal valve (not sealing properly), debris preventing valve closure.
- Solution: Clean the coupler thoroughly. If the leak persists, the valve mechanism may be damaged, requiring coupler replacement.
- Difficulty Connecting:
- Cause: Trapped pressure in the hydraulic line, damaged/bent coupler halves, dirt/debris on mating surfaces, thread damage (screw to connect types).
- Solution: Safely relieve trapped pressure before attempting connection (if possible). Clean mating surfaces thoroughly. Inspect for physical damage. Ensure threads are clean and undamaged. Using flat face couplers can sometimes mitigate issues with minor trapped pressure.
- Difficulty Disconnecting:
- Cause: System pressure still applied, bent locking sleeve or damaged threads, coupler connected under extreme pressure initially.
- Solution: Ensure system pressure is relieved. Inspect the locking mechanism/sleeve/threads for damage. Avoid connecting under high pressure.
General Maintenance Tips:
- Keep Clean: Always use dust caps and plugs when couplers are disconnected. Wipe flat face couplers clean before connecting.
- Inspect Regularly: Check for leaks, physical damage, wear, and corrosion.
- Connect/Disconnect Properly: Avoid forcing connections. Connect and disconnect hydraulic lines squarely. Do not use tools to hammer couplers together.
- Replace Worn Seals: Seals are wear items. Replace them as part of preventative maintenance, especially in demanding applications.
Proper maintenance makes quick work of attachment changes and significantly extends the life of your hydraulic quick couplings, preventing costly failures and ensuring the efficient operation of your hydraulic tools.
10. Are Hydraulic Quick Couplings Standardized Across Brands?
Interchangeability is a significant concern for users like Mark Thompson who manage fleets with equipment and attachments from various manufacturers. The good news is that there are international standards that many hydraulic quick coupler manufacturers adhere to, promoting compatibility. However, not all couplers are standardized, so it's crucial to verify.
- ISO 16028: This is the key standard for flat face hydraulic couplers. Couplers conforming to this standard from different manufacturers are generally interchangeable in terms of mating dimensions. This ensures that a male half from one brand will connect and function correctly with a female half from another brand, provided both meet the ISO 16028 specification for that coupling size.
- ISO 7241-1 Series A & B: These standards often apply to poppet valve couplers. Series A and Series B couplers are not interchangeable with each other, but couplers within the same series and size from different manufacturers are generally compatible if they conform to the standard. Series B is very common in North American agricultural machinery.
- Proprietary Designs: Some manufacturers produce couplers with unique, proprietary designs that are not interchangeable with other brands or standard types. This can lock users into a single supplier for replacements and additions.
- Threaded Couplers: While the thread types (NPT, BSP, etc.) might be standard, the overall coupling design for screw-to-connect couplers can vary significantly, often making them non-interchangeable between brands unless explicitly stated.
When purchasing new couplers or replacement halves, always confirm if they adhere to a specific ISO standard if interchangeability is required. Relying on a supplier like Bonovo, who understands these standards and can provide compatible hydraulic quick couplings, simplifies fleet management and ensures you can connect hydraulic hoses across your equipment efficiently. Checking for standard compliance is key to avoiding compatibility headaches when using hydraulic attachments.
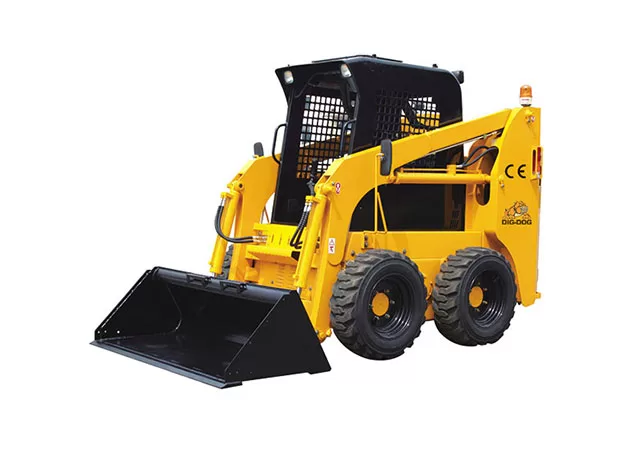
11. Why Partnering with a Quality Hydraulic Coupler Supplier Matters
Choosing the right hydraulic quick coupler goes beyond just matching specs; it involves selecting a reliable manufacturing partner. For businesses relying on heavy equipment, the performance and durability of components like quick couplers directly impact profitability. Downtime due to a failed coupling can halt operations, leading to project delays and significant costs – a major pain point for owners and fleet managers. This is why partnering with a specialized factory like Bonovo, focused on quality and reliability, is crucial.
A reputable supplier offers more than just a product:
- Quality Materials & Manufacturing: Using high-grade materials (like hardened steel) and precise manufacturing processes ensures the coupler withstands high pressure, wear, and harsh conditions, providing a reliable connection. Look for suppliers who emphasize durable construction.
- Technical Expertise: Experienced manufacturers understand the nuances of different types of hydraulic quick couplers and their applications. They can provide guidance on selecting the optimal coupler, thread type, and seal material for your specific needs, ensuring compatibility with machines like skid steer loaders or excavators.
- Product Range & Availability: A good supplier offers a wide variety of hydraulic couplers, including poppet, flat face, and threaded flat face types, in various different sizes and configurations, ensuring you can find the right fitting. Availability of spare parts and seals is also critical.
- Consistent Quality Control: Rigorous testing ensures each coupler meets performance and safety standards before it leaves the factory.
- Support & Communication: Clear communication and reliable after-sales support, including warranty information, address key concerns about sourcing from overseas suppliers.
Investing in quality hydraulic quick couplings from a trusted source like Bonovo minimizes the risk of premature failure, ensures safe operation, and maximizes the efficiency of your valuable construction equipment or agricultural machinery. It's about securing peace of mind alongside a dependable coupling. The right coupler ensures quick and secure connections for all your hydraulic applications.
Key Takeaways on Hydraulic Quick Couplers:
- Purpose: Hydraulic quick couplers allow fast, tool-free connection and disconnection of hydraulic lines, boosting productivity and versatility.
- Mechanism: They typically consist of male and female halves with internal valves that open upon connection and close upon disconnection to minimize fluid loss and contamination.
- Main Types: The most common types of hydraulic quick couplers are Poppet Valve, Flat Face (Flat-Face), and Threaded (Screw-to-Connect) couplers.
- Poppet Couplers: Economical and common, but prone to some spillage and contamination.
- Flat Face Couplers: Offer minimal spillage and contamination risk, easy to clean, and often adhere to ISO 16028 for interchangeability. Highly recommended for sensitive systems and demanding environments.
- Threaded Couplers: Provide the most secure coupling, ideal for very high pressure, vibration, and safety-critical applications.
- Selection Factors: Key considerations include operating pressure, flow rate, fluid type, port/thread size, application environment, and interchangeability needs.
- Maintenance: Regular cleaning, inspection, using dust caps, and replacing worn seals are vital for longevity and preventing leaks or connection issues.
- Standards: Check for compliance with ISO standards (like ISO 16028 for flat face) if interchangeability between brands is required.
- Supplier Choice: Partnering with a quality-focused manufacturer ensures durable, reliable couplers and provides necessary technical support.
Understanding and choosing the right hydraulic quick coupler is a small but critical detail that significantly impacts the efficiency, safety, and profitability of operating hydraulic machinery.