Understanding Hydraulic Quick Couplers: Types, Selection, and Benefits - Bonovo
Choosing the right equipment attachments can significantly impact your project's efficiency and profitability. Among the most vital components enabling versatility are quick couplers, especially hydraulic quick couplers. This article delves into the world of hydraulic quick couplers, exploring the different types available, how they function, and crucial factors to consider when selecting the right coupler for your machinery. Whether you manage a fleet of excavators, skid steers, or wheel loaders, understanding these components is key to maximizing uptime and getting the job done effectively. We'll cover everything from basic functions to specific types of hydraulic quick couplers, ensuring you have the knowledge to make informed decisions.
What Exactly is a Quick Coupler and Why Should I Care?
At its core, a quick coupler is a fitting designed to allow for the swift connection and disconnection of fluid lines, typically hydraulic or pneumatic, without the need for tools and with minimal fluid loss. Think about your job site: time is money. Swapping between a bucket, a grapple, or a hydraulic hammer needs to be fast. Quick couplers make this possible, transforming a single machine into a multi-tasking powerhouse. They are essential components for enhancing operational efficiency on construction equipment.
Imagine trying to manually unbolt and re-bolt heavy attachments multiple times a day. It's time-consuming, physically demanding, and increases the risk of contamination entering the hydraulic system. Quick couplers provide a convenient way to switch tasks rapidly, reducing downtime significantly. For fleet managers and company owners like Mark Thompson, this translates directly to improved productivity and profitability. A reliable quick coupler system means your expensive machinery spends more time working and less time being reconfigured. This simple coupling mechanism is a cornerstone of modern equipment versatility.
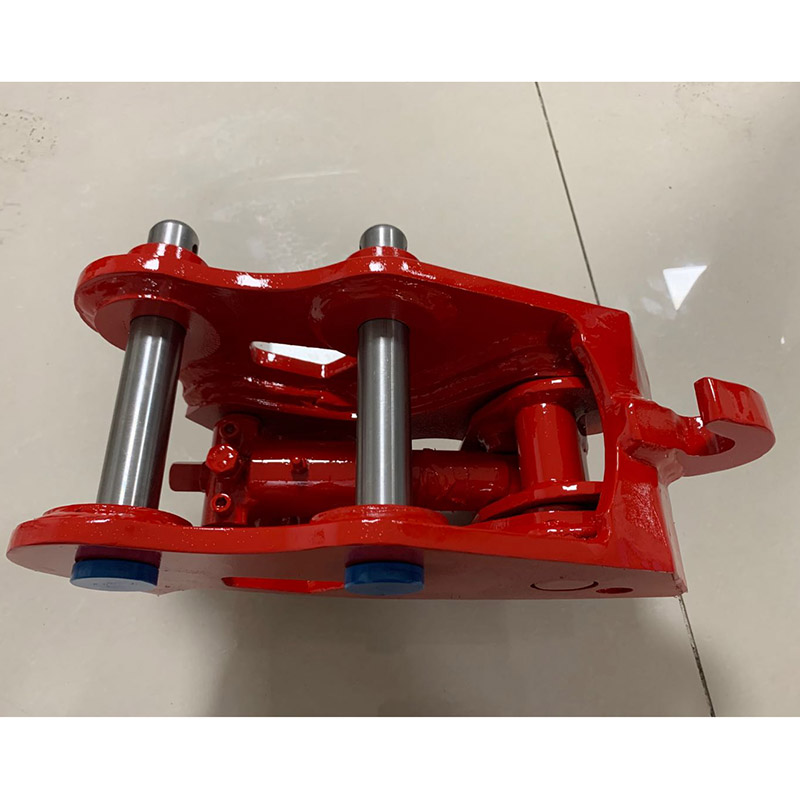
Understanding the Hydraulic Quick Coupler: How Does It Work?
A hydraulic quick coupler specifically handles hydraulic fluid, often under significant pressure. These couplers consist of two parts: a male plug and a female socket. When disconnected, internal valves in both halves automatically close, preventing hydraulic fluid from escaping and contaminants from entering the hydraulic system. When connected properly, these valves open, allowing the fluid to flow through the connection unimpeded, powering the attachment.
The primary function of a hydraulic quick coupler is to enable this quick connection and disconnection of fluid lines safely and efficiently. The locking mechanism ensures a secure connection that can withstand the operating pressure of the system. Different designs employ various locking methods (like balls, pins, or sleeves), but the goal is always a leak-free, reliable connection. Understanding this basic mechanism helps appreciate the importance of choosing a robust and well-engineered quick coupler for demanding applications. The internal valve design is critical to performance, affecting flow restriction and pressure drop across the coupling.
What Are the Main Types of Hydraulic Quick Couplers Available?
The world of hydraulic quick couplers isn't one-size-fits-all. There are various types designed for different applications, pressures, and environmental conditions. The most common distinction lies in the valve design used within the coupling. Understanding these differences is the first step in choosing the right quick coupler.
Here are the primary categories you'll encounter:
- Poppet Valve Couplers: These are a very common and often cost-effective type. They use a mushroom-shaped valve (poppet) backed by a spring. When disconnected, the spring pushes the poppet against a seat, sealing the coupling.
- Flat Face Couplers: As the name suggests, these feature a flat mating surface when disconnected. They use internal valves that seal before the coupling halves fully separate, minimizing spillage and air inclusion.
- Screw-to-Connect Couplers: These require threading the male and female halves together. They are known for their ability to handle very high-pressure and resist vibration, often used in heavy-duty applications. They can sometimes be connected under residual pressure.
- Specialty Couplers: This includes multi-couplers (connecting multiple hydraulic quick lines simultaneously), non-spill designs, and couplers made from specific materials like stainless steel for corrosion resistance.
Knowing these types of hydraulic quick couplers helps narrow down the options based on your specific needs, whether it's for an excavator, skid steer, or wheel loader attachment. BONOVO offers robust mechanical quick couplers that provide a foundation for many hydraulic setups.
Poppet vs. Flat Face Couplers: Which Type Suits My Application?
The choice between poppet and flat face quick couplers is a frequent decision point. Poppet couplers are often the traditional standard and can be more budget-friendly initially. They utilize poppet valves that seal against an internal seat. However, during connection/disconnection, there's a small space created that can allow minor hydraulic fluid leakage (spillage) and potential air ingress or contamination entry. The exposed poppet can also trap dirt.
Flat face couplers, on the other hand, are designed to minimize these issues. Their mating surfaces are flat when disconnected, which makes them easier to clean and less prone to trapping dirt. The valve design ensures minimal spillage during disconnection and minimal air inclusion during connection. This is crucial for sensitive hydraulic systems where contamination can cause significant damage and downtime. Flat-face quick couplings are often preferred in applications requiring high levels of cleanliness and safety, making them an excellent choice for many modern hydraulic solutions. While potentially having a higher upfront cost, the long-term benefits of reduced contamination and fluid loss often make flat face couplers more economical.
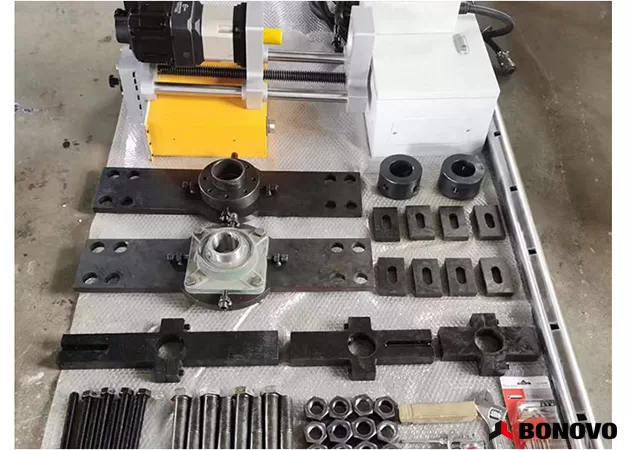
How Do I Safely Connect and Disconnect Hydraulic Couplers?
Safety and proper procedure are paramount when dealing with hydraulic systems, especially those under pressure. Improperly handling a quick coupler can lead to injury or equipment damage. Always follow the manufacturer's specific instructions, but here are general guidelines to connect and disconnect hydraulic lines safely:
- Relieve System Pressure: Before attempting to connect or disconnect any hydraulic quick coupler, ensure the hydraulic system pressure in that circuit is relieved. Trapped pressure can make connection difficult or impossible, and disconnection under pressure can be extremely dangerous, causing high-velocity fluid ejection.
- Clean the Couplers: Wipe both the male plug and female socket thoroughly with a clean, lint-free rag. Dirt or debris on the coupling surfaces is a primary source of hydraulic system contamination. This is especially critical for maintaining the integrity of flat face couplers.
- Align and Connect: Align the plug and socket carefully. For push-to-connect styles, push the plug firmly into the socket until the locking mechanism engages (often an audible click or the sleeve snaps into place). For screw-type, thread them together fully. Ensure the connection is secure.
- Disconnection: Again, ensure pressure is relieved. Retract the locking sleeve (if applicable) or unscrew the coupling. Pull the plug straight out of the socket. Immediately wipe both ends clean and consider using dust caps/plugs to protect the disconnected couplers provide.
Following these steps minimizes the risk of injury, fluid loss, and system contamination, ensuring your hydraulic quick couplers function reliably. Remember, never use your hands to check for leaks; use cardboard or wood instead.
Choosing the Right Hydraulic Quick Coupler: What Factors Must I Consider?
Selecting the optimal hydraulic quick coupler involves more than just picking a type. Several factors influence performance, longevity, and compatibility. For someone like Mark Thompson, focused on quality and value, considering these is crucial for making a sound investment. Here’s what to weigh when choosing the right quick coupler:
- System Pressure: What is the maximum operating pressure of your hydraulic system? The quick coupler must have a rated working pressure equal to or greater than your system's maximum. Also, consider pressure spikes (surges) that might occur.
- Flow Rate: How much hydraulic fluid needs to pass through the coupling per minute (GPM or LPM)? Choose a quick coupler size (thread size, internal passage diameter) that can handle the required flow without excessive pressure drop, which can cause heat and inefficiency.
- Fluid Compatibility: Ensure the coupling materials (body, seals, valves) are compatible with the type of hydraulic fluid used in your system (e.g., mineral oil, synthetic esters, water glycol). Incompatibility can lead to seal degradation and leaks.
- Operating Environment: Will the quick coupler be exposed to extreme temperatures, corrosive substances, excessive dust, or high vibration? This influences the choice of materials (e.g., steel, brass, stainless steel) and potentially the type of coupling (e.g., screw-to-connect for vibration).
- Connection Frequency: How often will the coupling be connected and disconnected? Heavy-duty applications with frequent changes might benefit from more robust designs like flat face or screw-type couplers.
- Potential for Connection Under Pressure: Some applications might encounter residual pressure. If connection under pressure is necessary, specific types of quick couplers are designed for this, often screw-type or specialized poppet designs.
- Spillage Tolerance: How critical is minimizing fluid spillage and air inclusion? For environmentally sensitive areas or clean operations, flat-face quick couplings are often the preferred hydraulic solutions.
Considering these factors such as the type of machinery and specific application ensures you select a quick coupler that delivers reliable performance and longevity.
Decoding the Specs: Pressure Ratings, Flow Rates, and Materials?
Technical specifications can seem daunting, but understanding them is key to choosing the right quick coupler. Let's break down the most important ones:
- Pressure Rating: Usually given in PSI (pounds per square inch) or Bar. This indicates the maximum continuous operating pressure the quick coupler is designed to handle safely. Always select a coupling with a rating exceeding your system's maximum working pressure. Burst pressure (the pressure at which it fails) is typically much higher (often 4:1 safety factor), but you should operate within the working pressure limit. High-pressure hydraulic systems demand appropriately rated couplers.
- Flow Rate: Expressed in GPM (gallons per minute) or LPM (liters per minute). This indicates the volume of hydraulic fluid the quick coupler can handle efficiently. Exceeding the rated flow can cause significant pressure drop (energy loss, heat generation) across the coupling, reducing system performance. The size of the hydraulic hoses and ports often dictates the required flow capacity.
- Materials:
- Body: Commonly steel (often plated for corrosion resistance), brass (good corrosion resistance, often used in lower pressure or specific chemical environments), or stainless steel (excellent corrosion resistance, used in harsh environments or for specific fluids).
- Seals: Nitrile (Buna-N) is common for standard hydraulic oils. Viton (FKM) is used for higher temperatures and broader chemical compatibility. Other materials like EPDM or PTFE may be used for specific properties.
- Valves: Typically hardened steel for durability in poppet and flat face designs.
Understanding these specifications allows you to compare hydraulic quick couplers effectively and ensure the one you choose meets the demands of your specific application and hydraulic system. Don't hesitate to consult manufacturer data sheets or speak with an engineer if you're unsure.
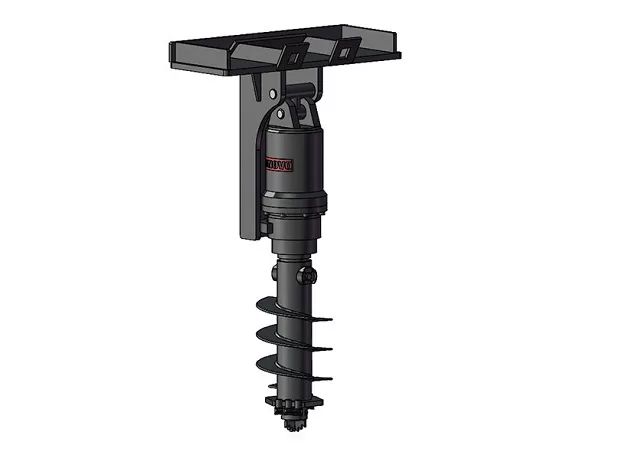
Will This Quick Coupler Fit My Excavator or Skid Steer? Ensuring Compatibility.
Compatibility is a major concern, and rightly so – a quick coupler that doesn't fit is useless. Compatibility involves several aspects:
- Machine Interface: If the quick coupler is part of a larger attachment system (like an excavator quick coupler that picks up buckets), it must match the machine's specific linkage (pin diameters, pin spacing, link width). Manufacturers like BONOVO design couplers for specific machine classes and models. Always verify the coupler's specifications against your machine's requirements. Our excavator buckets with thumbs often require specific hydraulic connections.
- Attachment Interface: If the hydraulic quick coupler is used to connect hydraulic hoses to an attachment (like a hammer or grapple), the thread type and size must match the ports on the attachment and the hydraulic hoses. Common thread types include NPT (National Pipe Taper), BSPP (British Standard Pipe Parallel), BSPT (British Standard Pipe Taper), JIC (Joint Industry Council), and ORFS (O-Ring Face Seal). Using adapters is possible but adds potential leak points.
- Interchangeability: Can a male plug from one brand connect to a female socket from another? Sometimes, yes, if they adhere to the same standard (e.g., ISO 16028 for flat face couplers, ISO 7241-A or -B for poppet types). However, mixing brands, even within the same standard, is often not recommended as slight tolerance differences can affect performance and sealing. It's generally best practice to use matched male and female halves from the same manufacturer.
Always double-check the connection types, thread sizes, and machine compatibility specifications before purchasing a hydraulic quick coupler. Providing your machine make and model, and the intended attachment, to the supplier (like us at BONOVO) helps ensure you get the right coupler the first time, preventing costly delays and frustration.
Maintaining Your Hydraulic Quick Couplers for Longevity and Performance?
Proper maintenance is key to extending the life of your hydraulic quick couplers and ensuring reliable operation. Neglect leads to leaks, contamination, connection difficulties, and premature wear. Here’s a simple maintenance routine:
- Keep Them Clean: This is the most crucial step. Always wipe couplers clean before connection and disconnection. Use dust caps and plugs on disconnected couplers and hose ends to prevent dirt ingress. Flat face couplers are easier to wipe clean.
- Inspect Regularly: Visually check couplers for damage (dents, cracks, deformed threads), corrosion, and worn seals. Check the locking mechanism for proper function. Look for leaks around the connection when pressurized.
- Lubricate (If Recommended): Some quick coupler designs may benefit from occasional lubrication of the locking mechanism or seals, using a lubricant compatible with the hydraulic fluid and seal material. Consult the manufacturer's guidelines.
- Replace Worn Seals: Leaking is often caused by worn or damaged seals. Seal kits are usually available. Replacing seals is far cheaper than replacing the entire quick coupler.
- Protect Threads: Ensure thread protectors are used when storing or transporting couplers or hoses to prevent damage.
- Avoid Side Loading and Impacts: Don't use the quick coupler connection as a handle or step. Avoid dropping them or subjecting them to impacts that could deform the body or valve. Prevent excessive twisting or side loading on the hydraulic hoses near the fitting.
Regular maintenance minimizes the risk of sudden failures, reduces the chance of hydraulic system contamination, and ensures smooth connection and disconnection, ultimately contributing to better operational efficiency and less downtime.
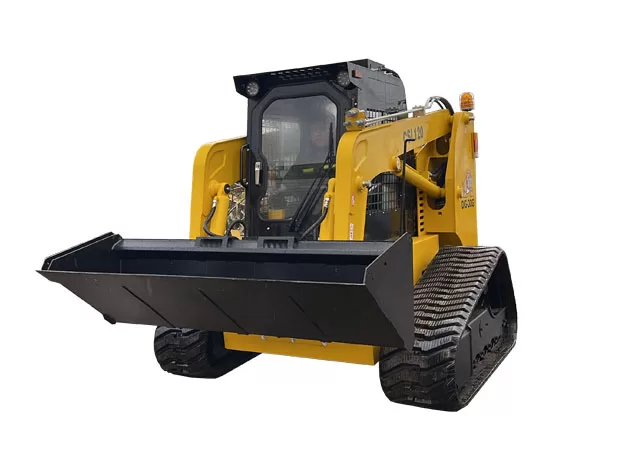
Troubleshooting Common Quick Coupler Problems to Minimize Downtime?
Even with proper maintenance, issues can arise. Knowing how to troubleshoot common quick coupler problems can save valuable time on the job site. Here are some frequent issues and potential causes:
- Difficulty Connecting:
- Cause: Trapped pressure in the line or attachment.
- Solution: Safely relieve the pressure before attempting connection.
- Cause: Dirt or debris on the coupling faces or in the locking mechanism.
- Solution: Thoroughly clean both halves.
- Cause: Damaged or deformed coupling body or thread.
- Solution: Inspect for damage; replace if necessary.
- Cause: Misalignment.
- Solution: Ensure the male and female halves are properly aligned before pushing or screwing together.
- Leakage When Connected:
- Cause: Worn or damaged seals.
- Solution: Replace the seals.
- Cause: Damaged valve or seat.
- Solution: Inspect; replace the quick coupler if internal damage is significant.
- Cause: Coupling not fully connected (locking mechanism not engaged).
- Solution: Ensure complete connection.
- Cause: Scored or damaged coupling mating surfaces.
- Solution: Replace the damaged half or both.
- Cause: System pressure exceeds the coupler's rating.
- Solution: Verify pressure and use an appropriately rated quick coupler.
- Leakage When Disconnected:
- Cause: Damaged or contaminated valve or seat preventing proper sealing.
- Solution: Clean thoroughly; replace the quick coupler if damaged.
- Difficulty Disconnecting:
- Cause: Trapped pressure.
- Solution: Relieve system pressure.
- Cause: Locking mechanism jammed with dirt or damaged.
- Solution: Clean; inspect for damage.
- Cause: Brinelling (indentation of locking balls/pins into the groove due to pressure spikes or excessive force).
- Solution: Replace the quick coupler.
Addressing these issues promptly helps reduce downtime and prevent further damage to the hydraulic system or other components. For persistent problems, consulting the manufacturer or a qualified hydraulic technician is recommended. Investing in high-quality hydraulic quick couplers from the start, like those designed for durability, can minimize these issues. Our skid steer augers rely on dependable hydraulic connections for powerful performance.
Why Partnering with a Specialized Manufacturer Matters for Your Quick Coupler Needs?
When sourcing critical components like hydraulic quick couplers, partnering with a knowledgeable manufacturer like BONOVO offers significant advantages, especially for discerning buyers like Mark Thompson. We aren't just selling parts; we understand the applications and the demands placed on construction equipment. As a factory specializing in attachments and machinery, we see firsthand how crucial reliable connections are.
A specialized manufacturer brings:
- Expertise: Deep understanding of materials (wear-resistant steel, brass, seal compounds), manufacturing processes, pressure dynamics, and compatibility requirements.
- Quality Control: Rigorous testing procedures ensure each quick coupler meets specifications for pressure holding, flow capacity, and durability. This minimizes the risk of premature failure and downtime.
- Customization & Compatibility: Ability to provide couplers tailored to specific machine models and applications, ensuring proper fit and function. We understand the nuances of matching couplers to excavators, skid steers like our CSL100, and wheel loaders.
- Technical Support: Access to engineers and technical staff who can assist with selection, troubleshooting, and provide detailed specifications. This overcomes communication pain points often experienced with general suppliers.
- Reliable Supply Chain: Consistent availability of products and spare parts (like seal kits), reducing lead time issues.
- Warranty & Service: Clear warranty terms and dependable after-sales support provide peace of mind.
Working directly with a manufacturer ensures you're getting a product designed and built for performance and longevity, backed by expertise. It's about investing in a reliable connection that enhances your equipment's value and operational efficiency, rather than just buying a fitting.
Key Takeaways on Hydraulic Quick Couplers:
- Efficiency Boost: Quick couplers dramatically speed up attachment changes, reducing downtime and increasing machine versatility.
- Hydraulic Focus: Hydraulic quick couplers are specifically designed to handle hydraulic fluid under pressure, using internal valves to prevent leaks and contamination.
- Know Your Types: Main types of hydraulic quick couplers include Poppet, Flat Face, and Screw-to-Connect, each with pros and cons. Flat face couplers excel at minimizing spillage and contamination.
- Selection is Crucial: Choosing the right quick coupler depends on system pressure, flow rate, fluid type, environment, and application needs. Match the specs carefully.
- Safety First: Always relieve pressure before connecting or disconnecting. Keep couplers clean to prevent contamination and ensure a secure connection.
- Compatibility Matters: Verify thread types, sizes, and machine interface compatibility to avoid costly mistakes.
- Maintain for Longevity: Regular cleaning, inspection, and timely seal replacement extend the life of your quick couplers.
- Partner Wisely: Working with a specialized manufacturer provides expertise, quality assurance, and reliable support for these critical components.
By understanding and properly utilizing hydraulic quick couplers, you can significantly enhance the productivity and profitability of your heavy equipment operations.