Steel Track vs Rubber Track: Making the Right Choice for Your Excavator or Mini Excavator - Bonovo
Choosing the right undercarriage for your construction machinery, whether it's a large excavator or a nimble mini excavator, is a crucial decision. The debate often boils down to steel track versus rubber track systems. Both have their place, but understanding the nuances can significantly impact your machine's performance, longevity, and your overall project profitability. As Allen from BONOVO, a factory specializing in manufacturing excavator attachments and machinery like mini excavators and skid steer loaders, I've seen firsthand how the right track choice influences efficiency. This article dives deep into the steel vs rubber tracks comparison, exploring rubber pads as a hybrid option, and helping you determine whether rubber or steel tracks are best suited for your specific needs, considering factors from terrain to operator comfort. We'll unpack the pros and cons, look at maintenance, and give you the insights needed to make an informed decision for your fleet.
What are the Fundamental Differences Between a Rubber Track and Steel Track?
At their core, both rubber track and steel track systems serve the same primary function: providing mobility and traction for heavy equipment like excavators, dozers, loaders, and skid steers. However, their construction and materials lead to vastly different characteristics. A steel track is composed of interconnected metal plates or track shoes, often with aggressive grousers (or cleats) for maximum grip. This traditional design is known for its sheer strength and resistance to harsh conditions. Think heavy-duty demolition or quarry work – that's prime steel track territory.
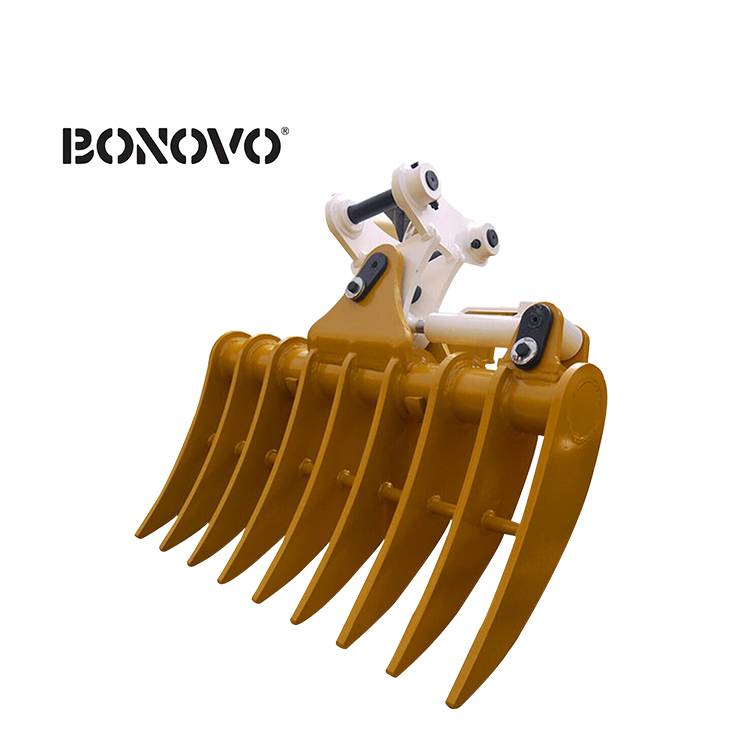
Conversely, a rubber track is typically a continuous loop of reinforced rubber composite, often embedded with steel cords for strength. This design significantly reduces ground pressure and minimizes surface damage. You'll commonly find rubber track systems on mini excavators, compact track loaders, and increasingly on mid-sized excavator models, especially where working on finished surfaces like pavement or lawns is necessary. The choice between steel or rubber fundamentally impacts where and how a machine can operate effectively. Understanding this basic difference is the first step in selecting the right undercarriage for your needs.
When Does Choosing a Rubber Track Make the Most Sense?
Opting for a rubber track system is often the best strategy when surface preservation is paramount. If your work involves landscaping, utility installation on existing properties, or operating on delicate surfaces like concrete driveways, asphalt pavement, or manicured turf, a rubber track is almost always preferred. Unlike a steel track, which can easily gouge and scar these areas, the rubber track distributes the machine's weight more evenly and provides a smoother, less damaging interface. This saves significant time and money on surface repairs after the job is done. For many contractors, especially those working in urban or residential settings, this is a major advantage.
Beyond surface protection, rubber track systems generally offer a smoother, quieter ride, enhancing operator comfort during long shifts. The flexibility of the rubber track helps absorb vibrations compared to the rigidity of steel track links. This can reduce operator fatigue and potentially increase productivity. Furthermore, rubber track machines often have slightly higher travel speeds and better traction on softer ground conditions like mud or sand compared to standard steel track designs, although specialized steel track patterns exist for such conditions too. Many mini excavator with rubber tracks models from brands like Kubota, Bobcat, and Yanmar are popular precisely for these reasons. A set of rubber tracks allows for versatility across various job sites without constant worry about surface damage.
Why Might You Prefer Steel Tracks for Heavier Applications?
When the going gets tough, steel tracks truly shine. Their inherent ruggedness makes them the go-to choice for demanding applications like heavy demolition, quarrying, forestry work involving sharp stumps and debris, and navigating extremely rocky terrain. A steel track can withstand impacts, abrasions, and penetration hazards that would quickly shred or puncture even the most robust rubber track. If your excavator or dozer consistently operates in environments where track damage is a high risk, the durability of steel offers significant long-term cost savings, despite potentially higher upfront costs for the undercarriage itself.

Moreover, steel tracks generally provide superior traction on uneven, hard surfaces and steep slopes due to their aggressive grouser designs (the protruding bars or 'cleats' on the track shoes). The individual track shoes can better conform to irregular ground, and the sharp edges of the grousers bite into rock or compacted earth. While the overall weight of steel adds to the machine's heft, this can be advantageous for stability and pushing power in heavy-duty tasks. For large excavators (think Komatsu, Hitachi, or larger Deere models) working in primary extraction or bulk earthmoving, operators often prefer steel for its brute force capability and resistance to extreme wear and tear. The disadvantage of surface damage becomes secondary to the need for raw power and longevity in these harsh conditions.
How Does Terrain Dictate the Steel vs Rubber Track Choice?
Terrain is arguably the single most important factor when choosing between rubber and steel tracks. As mentioned, finished surfaces like asphalt, concrete, or established turf strongly favor rubber track systems. Using a steel track here is asking for trouble – costly repairs and unhappy clients. Think about a mini excavator doing utility work in a backyard; a rubber track is essential. These tracks minimize ground pressure, reducing the likelihood of sinking in softer soils and leaving minimal trace on delicate surfaces.
Conversely, environments dominated by sharp rocks, demolition debris, scrap metal, or abrasive materials heavily favor steel tracks. A rubber track operating constantly in these conditions will likely have a drastically shortened lifespan due to cuts, tears, and chunking. Rocky terrain is particularly punishing for rubber track systems. Steel tracks, with their inherent toughness, simply endure this abuse far better. For mixed terrains, the decision becomes more nuanced. If a machine occasionally crosses pavement but primarily works in dirt or gravel, steel tracks might still be viable, perhaps with rubber pads (more on that later). However, if frequent transitions between harsh and sensitive surfaces occur, the versatility of a rubber track might outweigh its potential durability disadvantage in the rougher patches. Ultimately, you need to assess the predominant operating environment for your tracked equipment.
Can Rubber Pads on Steel Tracks Offer the Best of Both Worlds?
For operators who need the strength and longevity of a steel track but occasionally need to cross or work on sensitive surfaces, rubber pads offer a compelling hybrid solution. These pads, typically made from durable rubber compounds, bolt directly onto the steel track shoes. This creates a system that retains the robust steel track undercarriage structure while providing a protective rubber interface with the ground. Essentially, you get some of the surface protection benefits of a rubber track without sacrificing the core strength of steel. This concept is often seen as trying to achieve the "best of both worlds".

There are different types, including bolt-on pads (directly bolted to pre-drilled holes in the track shoe) and clip-on pads. Bolt-on rubber pads are generally more secure for sustained use. While they don't offer the exact same level of surface protection or quiet operation as a dedicated rubber track, they significantly reduce damage compared to bare steel tracks. The main disadvantage is the added cost and maintenance – pads can wear out or get damaged and need replacement. They also add weight and can sometimes trap debris between the pad and the shoe. However, for a machine like a mid-sized excavator that works on varied sites (e.g., road construction involving both dirt work and operating near finished pavement), rubber pads on a steel track system can be a very practical compromise, blending durability with surface-friendliness. These steel and rubber tracks combinations are quite popular.
Steel Tracks vs Rubber Tracks: Which Offers Better Durability and Lifespan?
When it comes to sheer resilience against harsh conditions and overall potential lifespan, steel tracks generally hold the advantage, especially in abrasive or high-impact environments. The durability of steel means it can withstand significant abuse from rocks, debris, and rough handling that would quickly degrade a rubber track. While individual steel track components like pins and bushings do wear out and require maintenance or replacement as part of the undercarriage system, the core track shoes can often last for thousands of hours, potentially being rebuilt or having grousers re-barred. The lifespan is heavily dependent on the operating conditions and maintenance practices, but in tough applications, steel tracks make a strong case for longevity.
Rubber track systems, while significantly improved over early iterations thanks to better compounds and internal steel cords, are inherently more susceptible to damage from sharp objects, excessive heat, and improper operation (like frequent sharp turns on abrasive surfaces). A single deep cut or tear can compromise the integrity of the entire track, often necessitating complete replacement, which can be costly and lead to downtime. However, in less aggressive environments like landscaping or utility work on softer ground or pavement, a high-quality rubber track can still provide excellent service life, often lasting 1000-2000+ hours. Aftermarket rubber tracks quality varies, so choosing a reputable supplier like BONOVO is crucial. Ultimately, the "better durability" depends on the application. For rock and demolition, steel tracks vs rubber is no contest for longevity. For general dirt work or sensitive surfaces, a rubber track can be durable enough and offers other benefits.
Durability Comparison Table:
Feature | Steel Track | Rubber Track |
---|---|---|
Abrasion Resistance | Excellent | Good to Very Good (Compound Varies) |
Cut/Puncture Resistance | Excellent | Fair to Good |
Impact Resistance | Excellent | Good |
Typical Lifespan (Harsh Env.) | Very High (Thousands of hrs) | Lower (Hundreds to ~1500 hrs) |
Typical Lifespan (Mild Env.) | Very High | Good (1000-2000+ hrs) |
Failure Mode | Gradual Wear (Pins, Bushings) | Catastrophic Cuts/Tears Possible |
Ideal Environment | Rocky, Demo, Abrasive Soils | Soil, Clay, Grass, Pavement |
How Critical is Tread Design in Rubber Track Performance?
Tread design is incredibly important for rubber track performance, influencing traction, wear life, ground disturbance, and even operator comfort. Unlike the relatively standard grouser bars on most steel tracks, rubber track manufacturers offer various tread patterns tailored to specific applications. A common style is the staggered block pattern, which provides a good balance of traction, smooth ride, and minimal ground disturbance, making it suitable for general use and work on turf or pavement. Another is the "C-lug" or straight bar tracks pattern, which offers more aggressive traction in loose materials like mud or clay but might cause slightly more surface marking and potentially a rougher ride.
The depth and spacing of the tread lugs also play a role. Deeper lugs generally provide better traction in soft conditions but might wear faster on hard surfaces. The specific rubber compound used in the rubber track tread affects both durability and grip. Some manufacturers offer specialized patterns, like zig-zag designs for enhanced lateral traction on slopes or low ground pressure tracks for extremely soft conditions. When selecting a rubber track, considering the primary operating conditions and matching the tread design accordingly can significantly enhance the machine with rubber tracks' effectiveness and provide a better experience for the operator. It's not just about choosing rubber vs steel; the type of rubber track matters.
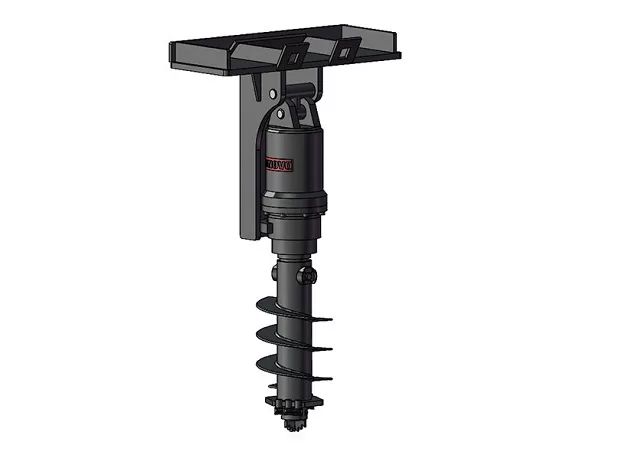
Considering Operator Comfort: Steel vs Rubber?
Operator comfort is a significant factor influencing productivity and fatigue, and there's a noticeable difference between steel track and rubber track systems. Generally, rubber tracks provide a much smoother and quieter ride. The inherent flexibility of the rubber material helps absorb vibrations and impacts from uneven terrain, reducing the jolts and noise transmitted to the operator's cabin. This is particularly noticeable when traveling at higher speeds or working on hard surfaces where steel tracks can generate considerable noise and vibration as the metal links articulate and contact the ground and undercarriage components like rollers and the sprocket.
Steel tracks, being rigid metal assemblies, transfer more ground shock and vibration directly through the machine's frame. While modern cabins offer good insulation, the difference is often still palpable, especially over a long workday. For operators spending hours in a mini excavator or compact track loader, the reduced fatigue associated with a rubber track can be a major benefit. Some might argue that on very rough, undulating terrain, the way steel tracks conform might feel more stable, but for overall vibration and noise levels, the rubber track typically offers a superior operator comfort experience. This is a key reason why rubber tracks dominate the mini-ex market and are increasingly popular on machines up to the medium excavator class where operator well-being is prioritized alongside performance.
What Maintenance Differences Should You Expect Between Rubber Track and Steel Track Systems?
Maintenance requirements differ significantly between rubber track and steel track undercarriages. Steel track systems require regular checks of track tension, inspection of pins, bushings, links, rollers, idlers, and the sprocket for wear, and periodic lubrication depending on the design (some are sealed and lubed). A critical maintenance task is managing track tension; improper tension (too tight or too loose) drastically accelerates wear on all undercarriage components. Eventually, components will wear out and require replacement, sometimes involving significant labor like turning pins and bushings or replacing entire link assemblies. While robust, steel track undercarriage maintenance is ongoing and can be labor-intensive.
Rubber track systems generally require less routine maintenance in terms of component lubrication (as there are fewer moving metal-on-metal parts like pins/bushings). However, maintaining correct tension is still crucial for rubber track life and preventing de-tracking. The primary maintenance focus shifts to regular inspection for cuts, tears, embedded objects, and excessive or uneven wear on the tread. Cleaning the undercarriage regularly is vital for both types but especially important for rubber track systems to prevent debris build-up that can accelerate wear or cause damage. The main disadvantage in rubber track maintenance is that significant damage often requires replacing the entire track, whereas a steel track can sometimes be repaired by replacing individual shoes or links. So, while daily checks might be simpler for rubber, the cost of major repairs (replacement) can be higher if severe damage occurs. Downtime can result from either system failing if maintenance is neglected.
Making the Final Call: Key Factors for Your Fleet (Bobcat, Kubota, Deere, Yanmar)
Choosing between rubber or steel tracks ultimately comes down to a careful evaluation of your specific operational needs, typical job sites, and budget. There's no single "best" answer; the optimal choice depends on your priorities. Whether you run Bobcat skid steers, Kubota or Yanmar mini excavators, or larger John Deere or Komatsu machines, consider these key factors:
- Primary Operating Surface: This is paramount. Frequent work on pavement, turf, or other delicate surfaces strongly favors rubber tracks. Working primarily in rocky terrain, demolition zones, or highly abrasive soil points towards steel tracks.
- Traction Requirements: While both offer good traction, steel tracks generally excel on hard, uneven ground and steep slopes due to aggressive grousers. Rubber tracks often perform better on softer ground and offer excellent grip on pavement or concrete, especially specialized rubber track tread designs. Consider conditions like mud, clay, ice and snow.
- Durability Needs vs. Budget: If maximum lifespan in harsh conditions is critical and surface damage is not a concern, the durability of steel is hard to beat, potentially offering lower long-term cost despite higher initial investment. If budgets are tighter or conditions less severe, high-quality rubber tracks can offer a good balance, but be prepared for potential replacement costs if significant damage occurs. Evaluate the cost of potential downtime associated with track failure.
- Operator Comfort & Noise: For applications where operator fatigue is a major concern or noise restrictions apply (e.g., urban environments), the smoother, quieter ride of rubber tracks is a significant advantage.
- Machine Size & Type: Mini excavators, compact track loaders (CTLs), and smaller dozers are commonly fitted with rubber tracks due to their typical applications. Larger excavators and dozers used in heavy-duty roles predominantly use steel tracks, sometimes with bolt on rubber pads as a compromise. Consider the machine's weight and intended tasks. A lighter machine like a mini excavator with rubber tracks exerts less ground pressure.
- Maintenance Resources: Assess your team's ability and willingness to perform the regular checks and potential repairs associated with each track system. Steel track maintenance can be more involved routinely, while rubber track replacement can be a larger, less frequent expense.
Many fleet managers, like our typical customer Mark Thompson, might find value in discussing specific needs with suppliers. As a manufacturer, we at BONOVO produce a wide range of Excavator Attachments and understand how track choice impacts attachment performance. Whether you need robust Rock Buckets for Wheel Loaders or versatile tools for a Mini Skid Steer Loader DSL30C, the undercarriage plays a key role. Consulting resources like an equipment forum or forum community dedicated to heavy equipment can also provide insights from other users' better experience scenarios.
Key Takeaways: Rubber vs. Steel Tracks
- Rubber Tracks: Best for sensitive surfaces (turf, pavement, concrete), offer better operator comfort (less noise/vibration), good traction on many surfaces (especially soft ground), common on mini excavators and CTLs. Main disadvantage is susceptibility to cuts/damage in harsh conditions.
- Steel Tracks: Superior durability in harsh, abrasive, or high-impact environments (rocky terrain, demolition), excellent traction on uneven/hard ground and slopes, preferred for large excavators and dozers. Main disadvantage is surface damage and higher vibration/noise.
- Rubber Pads on Steel Tracks: A hybrid option (bolt on pads) offering some surface protection while retaining steel track strength. A good compromise for mixed-use applications but adds cost and maintenance.
- Terrain is Key: The predominant operating environment is the most crucial factor in the decision.
- Tread Matters: For rubber tracks, the specific tread design significantly impacts performance.
- Maintenance Differs: Steel tracks require more routine component checks; rubber tracks require diligent inspection for damage, and replacement can be costly if significant damage occurs.
- No Single "Best": The right choice depends on balancing performance needs, operating conditions, budget, and operator comfort.
By carefully considering these points, you can make the most informed decision between steel or rubber tracks, ensuring your excavator, loader, or dozer is equipped for optimal performance and profitability on your job sites. If you need further assistance selecting machinery or attachments, don't hesitate to reach out to us at BONOVO.