Rubber Tracks vs. Steel Tracks for Excavators: Which Tread Wins? - Bonovo
Choosing the right tracks for your excavator is a crucial decision that impacts performance, cost, and the lifespan of your machine. This article breaks down the pros and cons of rubber tracks and steel tracks, helping you understand which option is best for your specific needs and applications. We'll explore everything from durability and traction to operator comfort, ensuring you make an informed choice.
When it comes to equipping your heavy equipment like excavators, the choice between rubber tracks and steel tracks can significantly influence your operational efficiency and project outcomes. Are rubber tracks the smoother operator, ideal for delicate surfaces? Or do steel tracks offer the rugged durability needed for tough terrains? Understanding the advantages and disadvantages of each track type is key. This guide dives deep into the world of rubber or steel tracks, helping you make the right call for your machine and your business.
What are the Key Advantages of Rubber Tracks for Mini Excavators with Rubber Tracks?
For mini excavators with rubber tracks, the benefits are often immediately apparent. Rubber tracks offer a significant advantage in terms of ground disturbance. Imagine working on a delicate lawn or surfaces like asphalt; rubber tracks provide a gentler footprint, reducing the risk of damage. This is a major plus for landscaping companies or projects in urban environments or residential areas. The smooth ride offered by rubber tracks also contributes to operator comfort, leading to a better experience and potentially increased productivity. Furthermore, machines equipped with rubber tracks generally produce less noise, making them suitable for noise-sensitive areas.
Another key advantage is the versatility of a machine with rubber tracks. They can move seamlessly between different types of ground without causing excessive damage. This eliminates the need for protective measures or switching between different track types for various job sites. The flexibility of the continuous track allows for excellent maneuverability, especially in tight spaces where mini excavators often operate.
When Do Steel Tracks Make More Sense for Heavy Equipment?
While rubber tracks excel in certain environments, steel tracks are the champions when it comes to sheer durability and rugged applications. For larger excavators and other heavy equipment working in demanding conditions like rocky terrain, construction sites with debris, or demolition projects with sharp objects, steel tracks give you better protection and longevity. The robust nature of steel tracks means they can withstand impacts and abrasions that would quickly damage rubber tracks.
Steel tracks generally offer superior traction in challenging conditions such as wet or muddy ground, or when dealing with steep inclines. The aggressive tread and cleat design bite into the earth, providing a secure grip. While they might not be ideal for pristine lawns, their ability to power through tough terrain makes them indispensable for many heavy-duty applications. Think of mining operations or forestry work where the terrain is unforgiving; here, the durability of steel tracks is paramount.
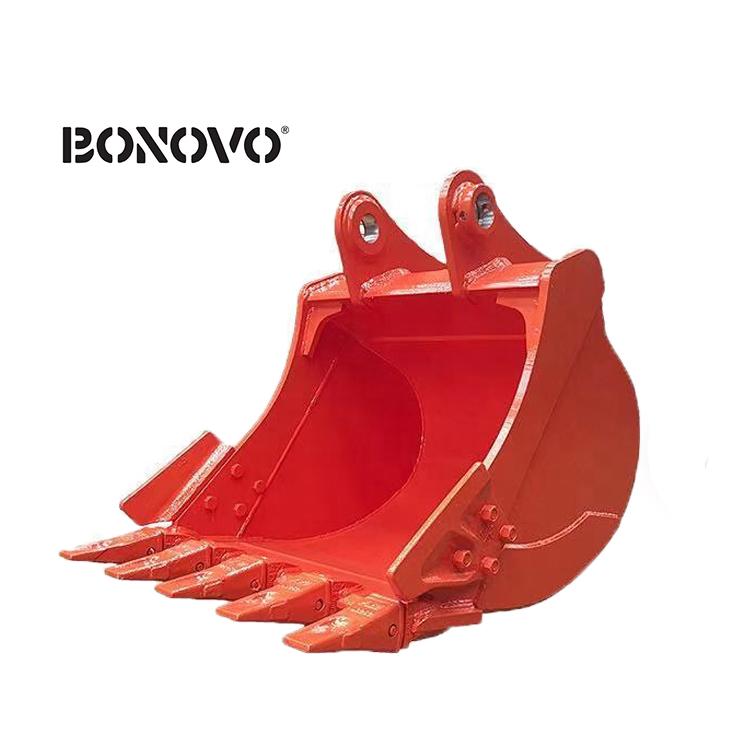
How Does Track Tread Affect Traction on Different Surfaces?
The tread pattern on both rubber and steel tracks plays a critical role in determining traction. A more aggressive tread with deeper lugs and a pronounced block pattern will provide enhanced grip in loose soil, mud, or snow. This is particularly important for steel tracks working in challenging environments. However, these aggressive treads can cause more damage to delicate surfaces like asphalt.
Rubber tracks, while generally less aggressive than steel tracks, also come in various tread patterns. Some rubber tracks feature a zig-zag or block pattern designed to maximize traction on softer surfaces while minimizing ground disturbance. For tasks like snow removal or working on slightly uneven terrain, a well-designed rubber track tread can offer a good balance between grip and surface protection. Ultimately, the best tread depends on the primary surfaces your excavator will be operating on.
What are the Disadvantages of Using Rubber Tracks?
Despite their advantages, rubber tracks do have some limitations. One significant disadvantage is their susceptibility to damage from sharp objects. Things like rebar, scrap metal, or even sharp rocks can cut or puncture rubber tracks, leading to costly repairs and downtime. While the technology is constantly improving, steel tracks inherently offer better resistance to punctures and cuts.
Another consideration is the lifespan of rubber tracks. While they can last a significant amount of time with proper maintenance, they generally don't have the same lifespan as steel tracks in harsh conditions. The constant friction and abrasion against rough surfaces can lead to wear and tear. Additionally, while they provide a smooth ride, rubber tracks may not offer the same level of stability as steel tracks when operating on very uneven or steep slopes.
What are the Disadvantages of Using Steel Tracks?
Steel tracks, while incredibly durable, also come with their own set of drawbacks. The most prominent disadvantage is the damage they can inflict on sensitive surfaces. Operating an excavator with steel tracks on asphalt or a well-manicured lawn is a recipe for disaster, leaving behind unsightly marks and potentially requiring costly repairs. This limits their versatility in certain applications.
Furthermore, steel tracks can create significant vibration and noise, which can be uncomfortable for the operator and disruptive in urban environments or residential areas. This can impact productivity and even lead to complaints on certain job sites. The lack of give in steel tracks also translates to a less smooth ride compared to rubber tracks, potentially leading to operator fatigue over long working hours.
How Does Durability Compare Between Rubber and Steel Tracks?
When it comes to pure durability, steel tracks generally have the edge, especially in demanding environments. They are built to withstand impacts, abrasions, and the rigors of heavy-duty work. However, the lifespan of both rubber and steel tracks depends heavily on the operating conditions and maintenance practices.
While rubber tracks might be more susceptible to cuts and punctures, advancements in materials and construction have significantly improved their durability. High-quality rubber tracks can offer impressive longevity if used in appropriate applications and properly maintained. Regular inspections, proper tensioning, and avoiding excessive contact with sharp objects can extend their lifespan considerably. Conversely, even steel tracks will wear down over time, requiring replacement of components like the cleats or the entire continuous track.
Which Track Type is Better for Protecting the Lawn and Sensitive Terrain?
For applications where minimizing ground disturbance is paramount, rubber tracks are the clear winner. Their flexible nature and wider surface area help to distribute the machine’s weight more evenly, resulting in significantly lower ground pressure compared to steel tracks. This makes them ideal for working on finished landscapes, golf courses, cemeteries, and other sensitive areas where preventing damage is crucial.
While skilled operators can minimize damage with steel tracks, the inherent design makes it challenging to avoid scuffing and marking on delicate surfaces. The aggressive tread and rigid structure of steel tracks simply aren't as forgiving as the compliant nature of rubber tracks when it comes to protecting the lawn and other sensitive terrain.
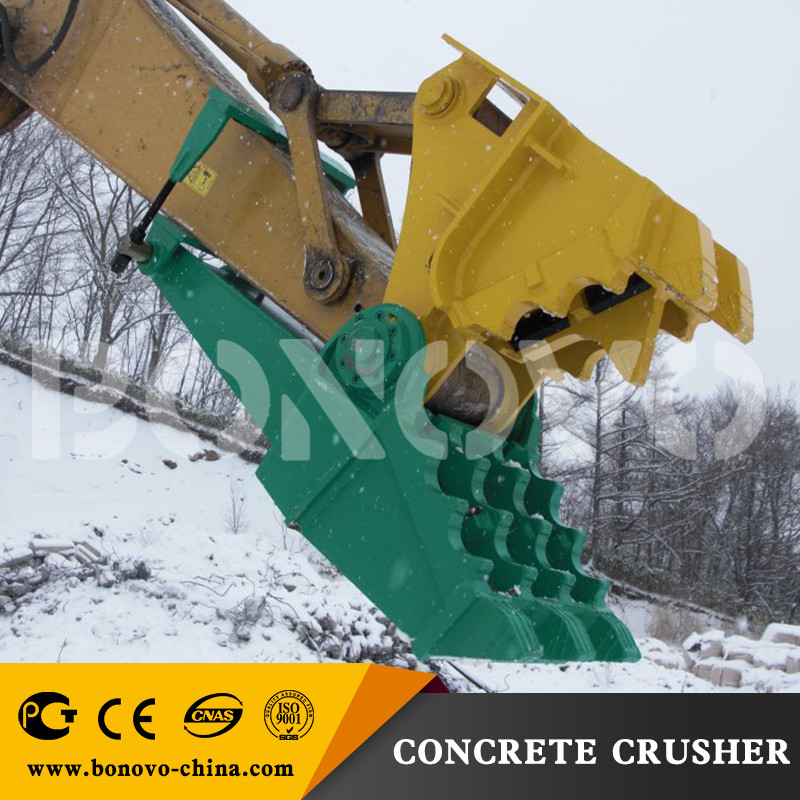
What About Rubber Pads on Steel Tracks: The Best of Both Worlds?
For those who need the durability of steel tracks but occasionally work on surfaces requiring more protection, bolt on rubber pads or clip-on rubber pads offer a versatile solution. These rubber pads attach to the steel tracks, providing a layer of cushioning that reduces ground damage when working on asphalt, concrete, or other sensitive areas.
Bolt on rubber pads offer a more permanent solution, while clip-on pads can be easily installed and removed as needed, providing flexibility for different job sites. This option allows you to maintain the traction and durability of steel tracks for tough jobs while having the ability to minimize damage when necessary. It's a popular choice for contractors who work in a variety of environments.
What are the Maintenance Requirements for Each Track System?
Both rubber and steel tracks require regular maintenance to ensure optimal performance and longevity. For rubber tracks, key maintenance tasks include checking and adjusting track tension, inspecting for cuts or damage, and ensuring the undercarriage is clean and free of debris. Proper tension is crucial to prevent premature wear and tear.
Steel tracks also require regular inspection for damage to the links, pins, and cleats. Lubrication of the pins and bushings is essential to reduce friction and wear. Keeping the tracks clean of packed mud and debris can also extend their lifespan. While rubber tracks might seem to require less maintenance initially, both systems benefit from proactive care.
Rubber or Steel: Making the Right Choice for Your Excavator?
Ultimately, the decision of whether to go with rubber or steel tracks depends on the work you primarily undertake. If your excavator spends most of its time on delicate surfaces or in noise-sensitive areas, rubber tracks are likely the better option, offering superior surface protection and operator comfort. The mini excavator with rubber tracks is a testament to this.
However, if your work involves harsh environments, demanding terrain, and a need for maximum durability and traction, steel tracks give you better long-term reliability. Consider the primary applications of your excavator, the types of surfaces you'll be working on, and the importance of factors like noise and ground disturbance. For some, rubber pads on steel tracks offer a valuable compromise. Carefully weighing the advantages and disadvantages of each system will lead you to the best choice for your specific needs and maximize the efficiency of your heavy equipment.
- Rubber Tracks: Best for delicate surfaces, noise-sensitive areas, and providing a smoother ride. Lower ground pressure minimizes damage.
- Steel Tracks: Ideal for harsh environments, rocky terrain, and applications requiring maximum durability and traction. More resistant to punctures and cuts.
- Rubber Pads on Steel Tracks: A versatile option offering a balance of durability and surface protection.
- Consider your primary job sites and the types of surfaces you'll be working on.
- Regular maintenance is crucial for extending the lifespan of both rubber and steel tracks.
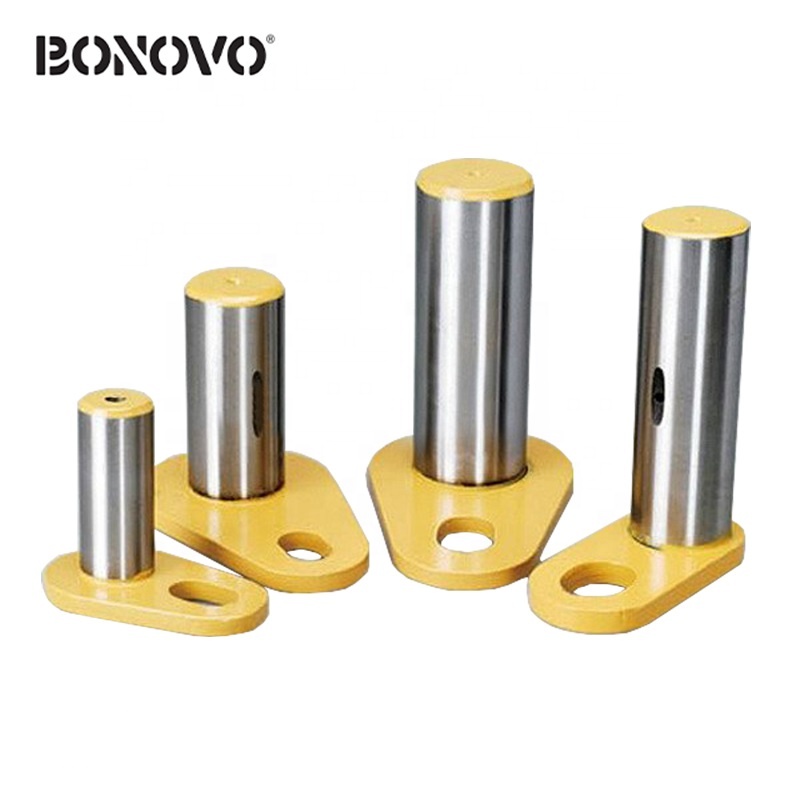
If you're looking to enhance the versatility of your excavator, consider exploring our range of high-quality excavator buckets. For quick and efficient attachment changes, our mechanical quick coupler is an excellent choice. And for tackling tough demolition tasks, our robust hydraulic hammers are built to last.