Excavator Thumbs Explained: Choosing Between Manual Thumb and Hydraulic Thumb Power - Bonovo
Ever watched an excavator try to pick up awkward objects like logs, rocks, or demolition debris? Sometimes the bucket just isn't enough. That's where an excavator thumb comes in, transforming your machine into a much more versatile tool. Think of it like adding a thumb to your excavator's hand (the bucket). This article dives deep into the world of excavator thumbs, explaining what they are, how they work, the crucial differences between a manual thumb and a hydraulic thumb, and which might be the best fit for your excavator and the jobs you tackle. Whether you're clearing land, handling materials, or involved in demolition, understanding the capabilities of a thumb attachment can significantly boost your excavator's productivity and make your operator's life much easier. Read on to discover how this simple yet effective attachment can make a big difference to your bottom line.
What Exactly is an Excavator Thumb Attachment?
An excavator thumb is essentially a heavy-duty metal attachment that mounts onto the excavator's stick (the arm part). It works in opposition to the excavator's bucket, much like your own thumb works against your fingers. This opposition creates a powerful clamping or gripping action. Without a thumb, an excavator bucket is primarily designed to dig and scoop loose material. Picking up larger, irregularly shaped items like boulders, tree stumps, pipes, or scrap metal can be clumsy, time-consuming, and sometimes impossible.
The thumb provides the necessary counter-force to securely grab and manipulate these objects. It allows the operator to pick, place, and sort materials with much greater precision and control. Whether it's a simple manual thumb or a more sophisticated hydraulic thumb, the core function remains the same: to significantly enhance the material handling capabilities of the excavator. Think of it as giving your powerful excavator the dexterity it needs for tasks beyond just digging. These thumbs are built using high-strength, wear-resistant steel to withstand the tough conditions they operate in.
As a factory specializing in excavator attachments, we see firsthand how adding a thumb transforms a standard excavator. It's one of the most popular attachment upgrades because the return on investment is often immediate through increased efficiency. A properly sized and installed thumb effectively turns your excavator into a multi-purpose machine, reducing the need for additional equipment on site for certain tasks. The thumb works seamlessly with your existing bucket, whether it's a standard digging bucket, a Trench Bucket for Excavator 1-80 Ton, or even a specialized rake.
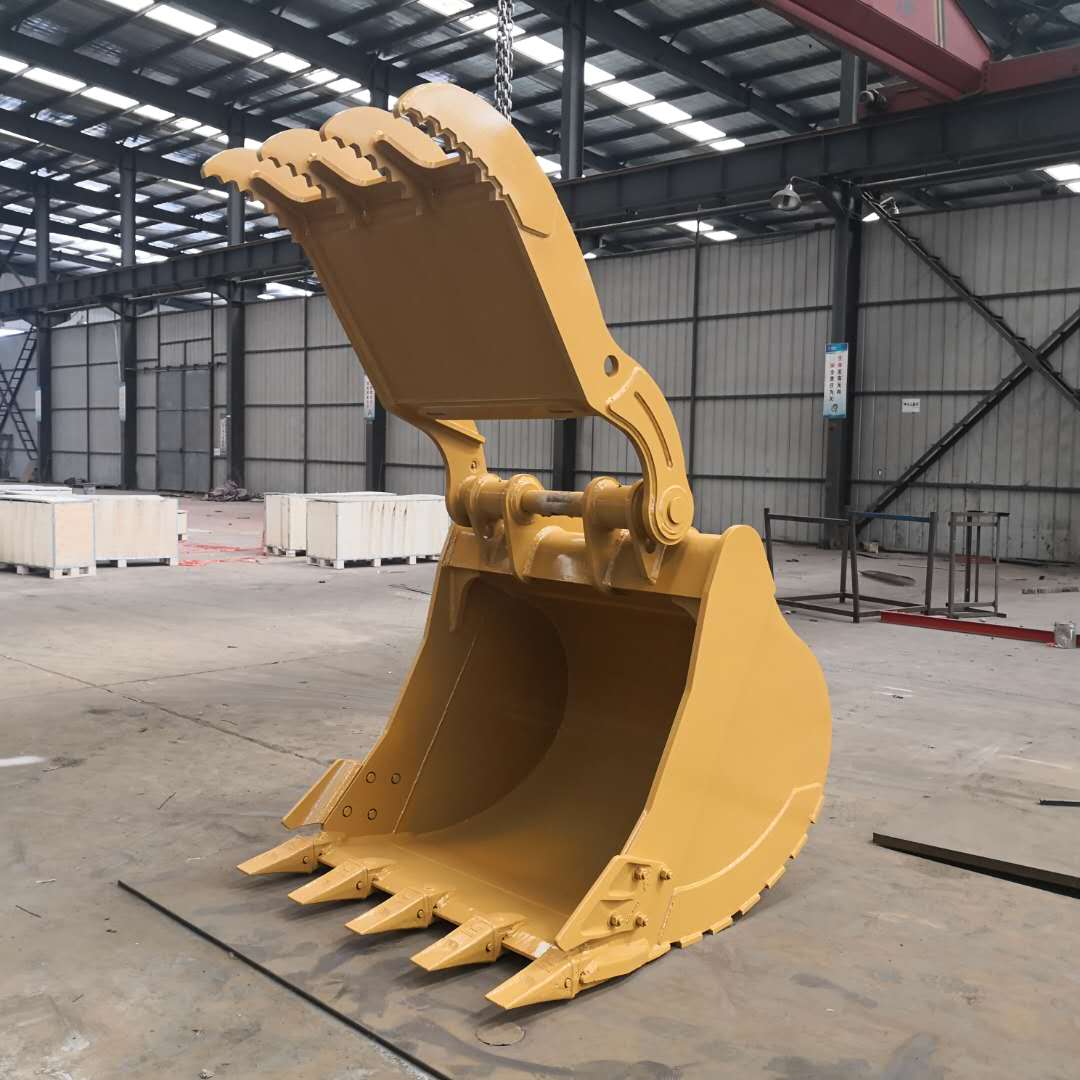
How Does an Excavator Thumb Work? The Basic Principle Explained.
The working principle behind an excavator thumb is straightforward: opposition. The thumb is mounted on the excavator’s stick, typically opposite the bucket. When the operator wants to grip an object, they curl the bucket inwards towards the stick, and the thumb either holds its position (in the case of a manual thumb) or is hydraulically moved towards the bucket (with a hydraulic thumb). This action traps the object securely between the bucket and the thumb.
Imagine trying to pick up a log with just an open hand versus using your thumb and fingers – the thumb makes all the difference. For an excavator, the thumb provides that crucial opposing force. The operator controls the bucket's movement as usual, and depending on the type of thumb, they either pre-set the manual thumb's position or use hydraulic controls (often a foot pedal or joystick button in the cab) to open and close the hydraulic thumb dynamically.
The effectiveness of the thumb work depends on the synchronization between the bucket's curl and the thumb's action. A hydraulic thumb offers the most control, allowing the operator to adjust the grip pressure and thumb position on the fly. A manual thumb, while simpler, requires the operator to physically change the pin position to adjust the gap between the thumb and the bucket teeth when fully curled. Regardless of the type, the goal is to create a secure clamp, enabling the excavator to lift, carry, and place objects that would be impossible to handle with the bucket alone.
Manual Thumb vs. Hydraulic Thumb: What's the Real Difference?
The fundamental difference lies in how the thumb is actuated or moved.
-
Manual Thumb: Sometimes called a fixed thumb or mechanical thumb, this type is simpler and generally less expensive. It consists of the thumb structure itself and usually a bracket welded or bolted to the excavator stick. The thumb typically has several holes allowing it to be pinned in different fixed positions relative to the stick. To adjust the thumb's working angle or to retract it fully against the stick when not needed, the operator must manually remove a pin, reposition the thumb, and reinsert the pin. It's effective for repetitive tasks where the object size doesn't vary much, but lacks on-the-fly adjustability. This manual adjustment process requires the operator to leave the cab.
-
Hydraulic Thumb: This type uses a hydraulic cylinder connected between the excavator stick and the thumb. The excavator's auxiliary hydraulic system powers this cylinder, allowing the operator to control the thumb's movement precisely from inside the cab using a joystick button or foot pedal. This enables the thumb to open and close dynamically, providing a much tighter and more adaptable grip on objects of varying shapes and sizes. A hydraulic thumb offers significantly more flexibility and efficiency compared to a manual thumb, especially for tasks involving sorting, demolition, or handling diverse materials.
Here's a quick comparison table:
Feature | Manual Thumb | Hydraulic Thumb |
---|---|---|
Actuation | Manual (pin adjustment) | Hydraulic Cylinder |
Control | Fixed positions | Variable, controlled from cab |
Adjustability | Requires getting out of the cab | On-the-fly from the cab |
Flexibility | Lower | Higher |
Efficiency | Good for consistent tasks | Excellent for varied tasks |
Cost | Lower initial cost | Higher initial cost |
Installation | Simpler (no hydraulics needed) | More complex (requires hydraulics) |
Best For | Budget-conscious buyers, simple repetitive grabbing tasks | Maximum productivity, varied materials, sorting, demolition |
Choosing between a manual thumb and a hydraulic one often comes down to budget, the type of work anticipated, and the desired level of convenience and efficiency. For operators like Mark Thompson, who value both quality and cost-effectiveness, understanding these differences is key. While the manual thumb offers affordability, the hydraulic thumb often pays for itself quickly through increased productivity, especially in demanding applications.
Which Excavator Thumb is Right for My Application? Matching the Thumb to the Task.
Selecting the right type of excavator thumb depends heavily on the primary application your excavator will be used for. There's no single "best" thumb – it's about finding the right match for your specific needs.
- For General Landscaping & Light Clearing: If you primarily handle brush, small logs, and occasional small rocks, a manual thumb might suffice. The objects are often similar in size, reducing the need for constant adjustment. Its simplicity and lower cost are attractive for lighter-duty use. You can set the thumb position for the typical material you handle and work quite effectively.
- For Heavy Land Clearing & Forestry: Dealing with large stumps, logs of varying diameters, and dense vegetation often requires the superior grip and adjustability of a hydraulic thumb. The ability to precisely control the thumb makes it easier to grab awkward stump roots or tightly stack logs. The power of the hydraulic thumb helps secure heavy loads safely.
- For Demolition & Scrap Handling: This application almost always demands a hydraulic thumb. Sorting through mixed debris, grabbing concrete slabs, twisting rebar, or loading scrap metal requires constant adjustment and precise control. The hydraulic thumb allows the operator to pick through piles, select specific items, and handle materials much faster and more safely than a manual thumb. A robust hydraulic thumb paired with a strong bucket is essential here.
- For Rock Placement & Hardscaping: Placing rock, boulders for retaining walls, or decorative landscape features requires precision. A hydraulic thumb excels here, allowing the operator to gently grab and accurately position heavy, irregular rock without damaging them. The fine control prevents dropping or fumbling, which is crucial for safety and aesthetics.
- For Utility Work & Pipe Handling: Laying pipe or handling other utility components often involves materials of a consistent diameter. While a hydraulic thumb offers the most flexibility, a well-positioned manual thumb can sometimes be adequate if the primary task involves handling similar-sized pipes repeatedly. However, the added safety and control of a hydraulic thumb are often preferred.
Consider the frequency of use and the variety of tasks. If you need a thumb only occasionally for simple tasks, a manual thumb is a cost-effective attachment. But if the thumb will be used daily for diverse and demanding jobs, the productivity gains from a hydraulic thumb will likely justify the higher initial investment. Think about the time saved by not having to constantly get out of the cab to adjust a manual thumb versus the seamless operation of a hydraulic thumb.
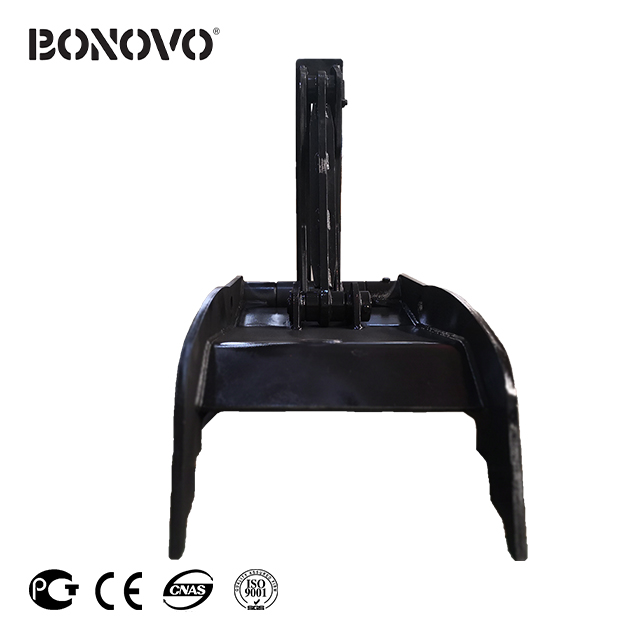
What are the Key Applications Showcasing Excavator Thumb Uses?
The versatility added by an excavator thumb opens up a wide range of applications, making the excavator a far more capable machine. Here are some key thumb uses:
- Land Clearing: This is perhaps the most common application. Thumbs are invaluable for removing trees, brush, and stumps. They allow the operator to easily grab, lift, and pile vegetation. A hydraulic thumb is particularly effective for extracting stubborn stump roots by gripping them while the bucket digs underneath. It makes clearing land significantly faster.
- Demolition: In demolition projects, excavator thumbs (almost always hydraulic thumbs) are used for sorting C&D waste (concrete, wood, metal), tearing down structures by grabbing beams or walls, and loading debris into trucks or crushers. The precise control helps separate recyclable materials.
- Material Handling: Loading and unloading irregularly shaped materials like pipes, logs, scrap metal, or large rocks is much safer and more efficient with a thumb. The thumb secures the load against the bucket, preventing items from rolling or falling during transport.
- Rock and Boulder Placement: Landscapers and construction crews use thumbs for building retaining walls, placing decorative boulders, or creating erosion control structures. A hydraulic thumb allows for careful placement without damaging the rock.
- Waste Handling and Recycling: Transfer stations and recycling facilities use excavators equipped with thumbs (often grapple-style thumbs) to sort and move various types of waste materials.
- Forestry: Beyond basic land clearing, thumbs are used in logging operations for loading logs onto trucks, stacking timber, and handling slash.
- Septic System Installation: Placing septic tanks and handling associated materials like pipes and gravel bags is simplified using the thumb.
Essentially, any task that requires your excavator to securely grab, lift, place, or sort objects beyond simple scooping can benefit immensely from the addition of a thumb. It transforms the excavator from just a digging machine into a versatile material handler. We've seen customers use our thumbs for everything from delicate boulder placement to aggressive stump removal.
Can a Hydraulic Thumb Really Boost My Machine's Efficiency?
Absolutely. While a manual thumb adds capability, a hydraulic thumb significantly amplifies an excavator's overall efficiency and productivity in several key ways:
- Reduced Cycle Times: The ability to instantly adjust the thumb from the cab saves considerable time compared to manually repositioning a manual thumb. The operator doesn't need to stop working, get out, change the pin position, and get back in. This seamless operation keeps the machine working continuously, especially crucial when handling materials of varying sizes.
- Improved Sorting Capabilities: Sorting mixed materials (like in demolition or site cleanup) is much faster with a hydraulic thumb. The operator can quickly open, close the bucket, and adjust the thumb position to selectively grab desired items from a pile, rather than clumsily trying to scoop and separate with just the bucket.
- Enhanced Material Handling: A hydraulic thumb provides a more secure and adaptable grip on objects. This reduces the chance of dropping materials, which saves time and improves safety. The operator can confidently lift and move awkward items like logs, pipes, or concrete chunks, often handling larger or more complex pieces than possible with a manual thumb or bucket alone.
- Increased Versatility: A hydraulic thumb makes the excavator proficient at a wider range of tasks. This can potentially reduce the need for other specialized equipment on site (like a separate material handler or skid steer with a grapple), lowering overall project costs and logistical complexity. One machine can dig, grab, sort, and load more effectively.
- Operator Comfort and Focus: Eliminating the need for the operator to frequently leave the cab to adjust a manual thumb not only saves time but also reduces fatigue and keeps the operator focused on the task at hand. This contributes to safer and more consistent performance throughout the workday. You can work more efficiently when you aren't constantly interrupting the workflow.
While the initial cost of a hydraulic thumb is higher, the return on investment through boosted productivity, reduced labor time (no need to get out and adjust), and increased machine utilization often makes it a very worthwhile upgrade for businesses aiming for maximum efficiency. For fleet managers like Mark Thompson, maximizing the work output per hour for each machine is critical, and a hydraulic thumb directly addresses this need.
How is a Manual Thumb Positioned and Adjusted?
Adjusting a manual thumb (also known as a mechanical thumb or stiff thumb) is a straightforward, albeit manual, process. Unlike a hydraulic thumb that uses a cylinder, a manual thumb relies on a pin and a series of pre-drilled holes to set its working position.
Here’s the typical process:
- Safety First: Ensure the excavator is parked on level ground, the engine is off, and the hydraulic pressure is relieved (lower the attachment to the ground).
- Identify Components: Locate the thumb structure, the mounting bracket on the excavator stick, and the pin that holds the thumb in place. There will also be a stowage position bracket or hole, usually allowing the thumb to fold tightly against the stick when not in use.
- Remove the Pin: Use appropriate tools (hammer, punch if necessary) to remove the locking mechanism (like a linchpin or bolt) and then drive out the main pin connecting the thumb to its adjustment bracket or link.
- Reposition the Thumb: Swing the manual thumb to the desired working position. Most manual thumbs offer 3-5 different positions. A position closer to the bucket teeth provides a tighter grip for smaller objects, while a position further away allows for grabbing larger items. You can also swing it back to the stowed position if you need to do extensive digging without the thumb interfering.
- Reinsert the Pin: Align the hole in the thumb with the desired hole in the bracket/link. Insert the main pin fully. It might require some wiggling or a tap with a hammer.
- Secure the Pin: Reinstall the locking mechanism (linchpin, bolt, etc.) to ensure the main pin cannot accidentally fall out during operation.
This manual adjustment needs to be performed every time the operator needs a different working angle or wants to stow the thumb. While effective for its purpose, it's the primary drawback compared to the convenience of a hydraulic thumb. The quality of the pin and the ease with which it can be removed and inserted are important factors in a good manual thumb design. Look for manufacturers who supply high-strength, properly sized Excavator Bucket Pins as part of the thumb kit.
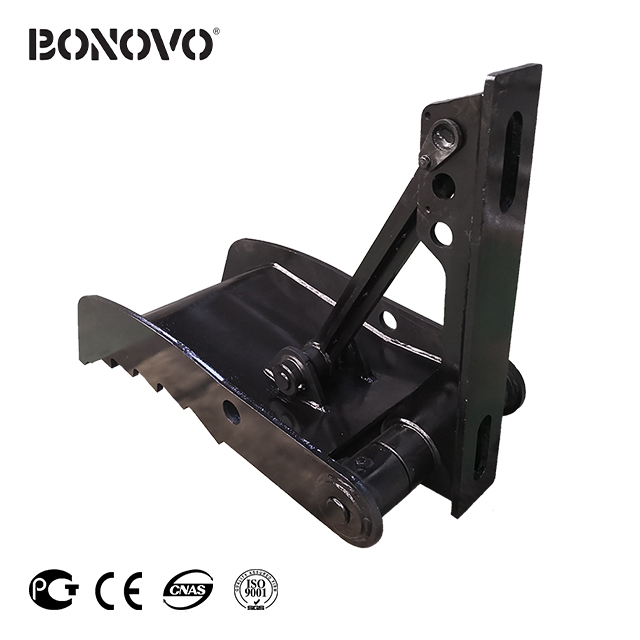
Progressive Link vs. Standard Hydraulic Thumb: Is There an Advantage?
When discussing hydraulic thumbs, you might encounter the term "progressive link thumb" (or "linkage thumb"). This design differs slightly from a standard direct-pinned hydraulic thumb.
-
Standard Hydraulic Thumb: In the most common setup, the hydraulic cylinder connects directly from a mounting point on the excavator stick to a mounting point on the thumb itself. As the cylinder extends and retracts, it pivots the thumb directly. This provides a consistent force throughout the thumb's range of motion.
-
Progressive Link Thumb: This design incorporates an additional linkage system between the cylinder, the stick, and the thumb. This linkage changes the geometry as the thumb moves, resulting in a wider range of motion (often up to 180 degrees or more of rotation) compared to a standard thumb. Furthermore, the progressive link mechanism can increase the thumb's gripping force, particularly when it's closer to the bucket, providing more power at the start and end of the closing arc.
Advantages of a Progressive Link Thumb:
- Increased Rotation: The most significant advantage is the extended range of motion. This allows the thumb to retract further out of the way when digging and potentially grab objects closer to the excavator's stick.
- More Consistent Clamping Force: The linkage helps maintain a more consistent clamping force throughout the rotation cycle, potentially improving grip on oddly shaped items.
- Potentially Higher Grip Force: The mechanical advantage provided by the progressive link can sometimes result in a stronger grip compared to a standard hydraulic thumb using the same size cylinder.
Disadvantages:
- Complexity: More moving parts (pins, links, bushings) mean more potential wear points and slightly more complex maintenance.
- Cost: Progressive link thumbs are generally more expensive than standard hydraulic thumbs due to the additional components and engineering.
- Bulk: The linkage system can sometimes add more bulk to the side of the excavator stick.
For most general applications, a standard hydraulic thumb provides excellent performance and flexibility. However, for operators needing the maximum possible rotation, the ability to pick items very close to the stick, or potentially higher grip force, a progressive link thumb might be a worthwhile upgrade. Evaluate if the added complexity and cost are justified by the specific tasks you perform. The progressive link thumb offers enhanced dexterity for certain specialized operations.
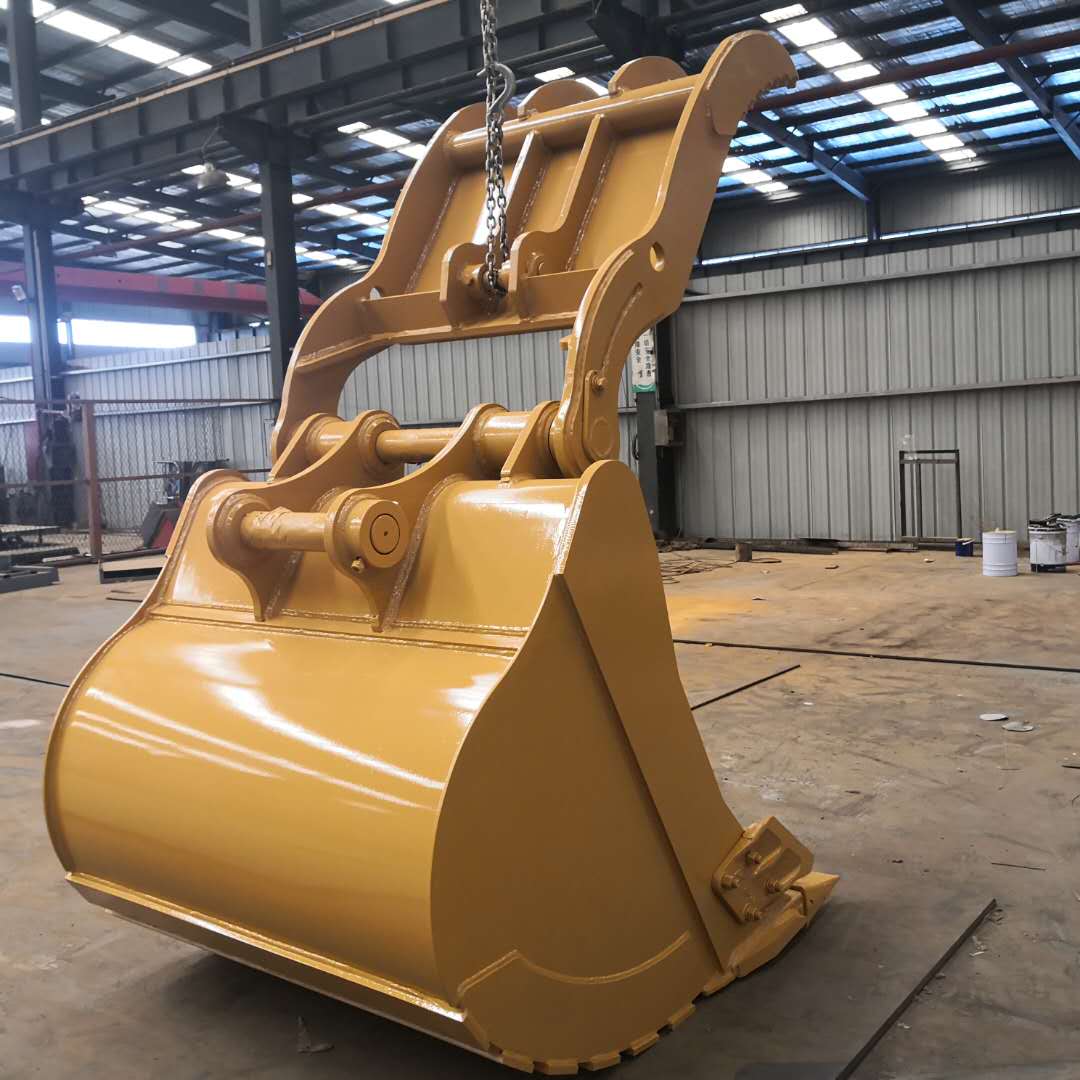
What Should I Look For When Buying an Excavator Thumb? (Quality, Compatibility)
Choosing the right excavator thumb involves more than just deciding between manual and hydraulic. Quality, compatibility, and design features are crucial for ensuring longevity, performance, and safety. Here's what buyers like Mark Thompson, who are quality-sensitive yet seek value, should consider:
- Material Quality: Look for thumbs constructed from high-strength, abrasion-resistant steel (like AR400 or AR500 steel, especially for the tines that contact material). This ensures the thumb can withstand the demanding conditions of digging, grabbing rock, and handling abrasive debris without excessive wear or bending. Ask the manufacturer about the specific steel grades used.
- Build Quality & Welds: Inspect the quality of the weld joints. Clean, consistent, and deep-penetrating welds are essential for structural integrity. Poor welds are common failure points. Look for reinforcements in high-stress areas. A robust build is non-negotiable.
- Compatibility: This is critical. The thumb must be correctly sized for your specific excavator make and model (considering weight class, stick width, and bucket size). It also needs to be compatible with your excavator's existing bucket and quick coupler (if used).
- Stick Mount: Ensure the mounting bracket fits the profile and width of your excavator’s stick. Some thumbs require welding the main bracket, while others offer bolt-on options.
- Bucket Synchronization: The thumb needs to mesh properly with the excavator’s bucket teeth or cutting edge when closed. The length and curvature of the thumb tines should complement the bucket's arc to provide a good grip without interference. The distance between the main bucket pin and the thumb mounting pin is a crucial measurement.
- Hydraulics (for Hydraulic Thumbs): Confirm your excavator has the necessary auxiliary hydraulic lines and that the thumb's cylinder operating pressure and flow requirements match your machine's specifications.
- Pin Quality: For both manual and hydraulic thumbs, the pins are critical components. Ensure they are made from hardened steel and are the correct diameter and length for a secure fit without excessive play. Easy-to-use locking mechanisms are also important for manual thumb pins.
- Thumb Design:
- Tine Shape & Spacing: Wider, serrated tines offer a better grip on larger objects like logs or boulder. More numerous, narrower tines might be better for handling loose brush or smaller debris.
- Curvature: The arc of the thumb should ideally follow the arc of the bucket as it curls.
- Stowage: Ensure the thumb retracts tightly against the stick and doesn't obstruct visibility or normal digging operations when not in use.
- Warranty and Support: Understand the manufacturer's warranty terms. Does it cover structural failure? Are spare parts (like seals for hydraulic thumbs, pins, bushings) readily available? Good after-sales support is vital, especially when buying internationally.
Don't just focus on the lowest price. A cheap, poorly made thumb can fail quickly, leading to costly downtime and potential safety hazards. Investing in a well-engineered, robust thumb from a reputable manufacturer will pay off in the long run through reliability and performance. Always provide your exact excavator model and bucket details when ordering a thumb to ensure proper fitment.
Why Source Your Excavator Thumb Directly from a Factory Like Bonovo?
For experienced buyers like Mark Thompson, sourcing attachments directly from a specialized factory like Bonovo in China offers several compelling advantages, addressing key concerns about quality, cost, and reliability:
- Cost-Effectiveness: Bypassing intermediaries and dealing directly with the factory often results in more competitive pricing. We operate multiple production lines efficiently, allowing us to offer high-quality excavator thumbs (both manual thumb and hydraulic thumb models) at attractive price points without compromising on materials or construction. This aligns with the preference for quality alongside competitive pricing.
- Quality Control: As the manufacturer, we have direct oversight over the entire production process – from raw material sourcing (using high-grade, wear-resistant steel) to welding, machining, assembly, and final inspection. This ensures consistent quality and adherence to design specifications. We understand the demanding conditions these thumbs face in North America, Europe, and Australia, and build them accordingly.
- Customization Capabilities: Need a thumb with a specific tine configuration, a unique mounting bracket, or tailored to match a non-standard bucket? A direct factory relationship makes custom modifications easier. We can often accommodate specific requirements based on your technical drawings or detailed specification requests.
- Direct Communication & Technical Expertise: Communicating directly with the factory means you're talking to people who understand the product intimately. Our team (like myself, Allen) can provide detailed technical information, answer compatibility questions accurately, and address concerns efficiently, minimizing the communication frustrations sometimes encountered with suppliers. We know excavators, we know attachments, and we know thumbs.
- Transparency & Reliability: We welcome factory visits and audits, providing transparency into our operations. Building long-term relationships with clients like Mark is important to us. We focus on clear communication regarding lead times, shipping, and provide reliable after-sales support, including warranty service and spare parts availability (like pins, bushings, cylinder seals for hydraulic thumbs). This directly tackles pain points regarding supplier reliability and support. Check out our range of reliable Backhoe mechanical thumb from BONOVO for wholesale and retail.
- Wide Product Range: Beyond just thumbs, we manufacture a comprehensive range of excavator attachments (buckets, grapples, quick couplers, rippers), skid steer attachments, wheel loader attachments, and ground engaging tools. Sourcing multiple products from a single, trusted factory can streamline procurement and logistics.
Choosing a direct factory supplier like Bonovo provides access to quality products, technical expertise, and competitive pricing, mitigating many common purchasing concerns for international buyers.
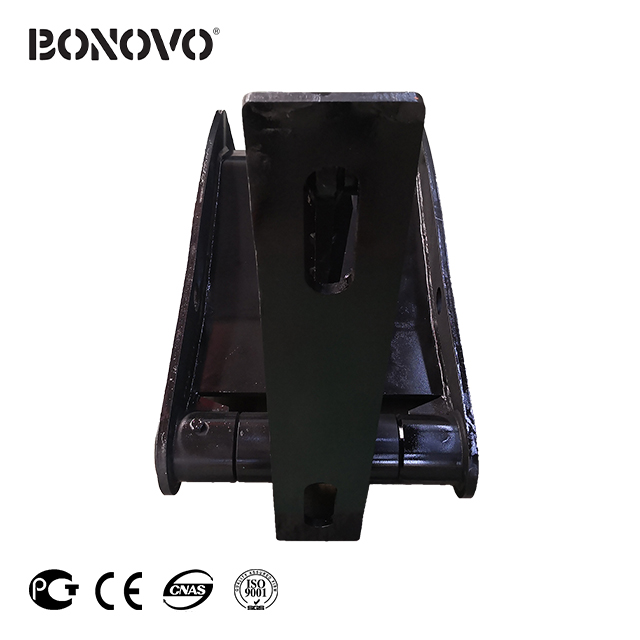
Essential Installation and Maintenance Tips for Your Excavator Thumb
Proper installation and regular maintenance are key to ensuring your excavator thumb performs reliably and safely for years to come.
Installation:
- Safety First: Always follow safety procedures. Park the excavator on stable ground, lower the attachment, turn off the engine, and relieve hydraulic pressure before starting work.
- Mounting Bracket: If your thumb requires welding the main bracket to the excavator stick, ensure it's done by a qualified welder following the manufacturer's guidelines regarding placement and weld procedure. Proper alignment is crucial. Bolt-on brackets should be torqued to the correct specifications.
- Attaching the Thumb: Carefully lift the thumb into position (it can be heavy!). Align the pivot holes and insert the main pin. Secure the pin.
- Hydraulic Connections (Hydraulic Thumb): Connect the hydraulic hoses from the thumb's cylinder to the excavator's auxiliary hydraulic circuit. Ensure connections are clean and tight to prevent leaks. Route hoses carefully to avoid pinching or rubbing during operation. Verify the flow direction is correct for proper thumb open and close function via the operator controls.
- Manual Thumb Linkage: For a manual thumb, ensure the positioning link (if equipped) is correctly installed and that the pin fits snugly in the adjustment holes.
- Function Test: Start the excavator and slowly test the full range of motion for both the bucket and the thumb. Check for any interference, binding, or hydraulic leaks. Ensure the thumb retracts properly to its stowed position.
Maintenance:
- Regular Inspection: Visually inspect the thumb daily or before each use. Look for cracks (especially around welds), bent tines, loose bolts, or hydraulic leaks. Check the condition of pins and bushings for wear.
- Greasing: Regularly grease all pivot points (main thumb pin, cylinder pins, linkage pins on progressive link thumbs) according to the manufacturer's recommendations (often daily or every 8-10 operating hours). Proper lubrication prevents premature wear of pins and bushings.
- Hydraulic System (Hydraulic Thumb): Check hydraulic hose condition regularly for wear, cracks, or leaks. Ensure hydraulic fluid levels are adequate. Monitor the cylinder seals for any weeping or leaks.
- Pin Security: For manual thumbs, regularly check that the locking mechanism for the adjustment pin is secure. For all thumbs, ensure the main pivot pin retainers are in place and tight.
- Cleaning: Keep the thumb relatively clean, especially around pivot points and hydraulic components, to make inspections easier and prevent debris buildup.
- Component Replacement: Replace worn pins, bushings, or damaged hydraulic components promptly to prevent further damage and ensure safe operation. Using genuine or high-quality replacement parts is recommended.
Following these simple steps will help maximize the life and performance of your excavator thumb attachment, whether it's a hardworking manual thumb or a versatile hydraulic thumb.
Key Takeaways: Elevate Your Excavator's Capabilities with a Thumb
Adding an excavator thumb is one of the most impactful upgrades you can make to your machine. Here’s what to remember:
- Function: An excavator thumb works opposite the bucket to provide a secure gripping action, dramatically increasing material handling versatility.
- Types: Choose between a simpler, lower-cost manual thumb (requires manual pin adjustment) and a more versatile, efficient hydraulic thumb (controlled from the cab).
- Hydraulic Advantage: A hydraulic thumb significantly boosts productivity through on-the-fly adjustments, better sorting, and reduced cycle times, making it ideal for varied tasks, demolition, and maximizing efficiency.
- Application Matters: Match the thumb type (manual vs. hydraulic, standard vs. progressive link) to your primary tasks – light clearing may suit a manual thumb, while heavy demolition demands a hydraulic thumb.
- Quality is Key: Invest in a robust thumb made from high-strength steel with quality welds and correctly sized, hardened pins. Compatibility with your specific excavator and bucket is crucial.
- Factory Direct Benefits: Sourcing from a specialized factory like Bonovo can offer cost savings, quality control, customization options, and direct technical support.
- Maintenance: Regular inspection, greasing, and prompt repair of worn components are vital for the longevity and safe operation of any excavator thumb.
By understanding the options and benefits, you can equip your excavator with the right thumb attachment to tackle more jobs, work more efficiently, and ultimately improve your operational profitability.